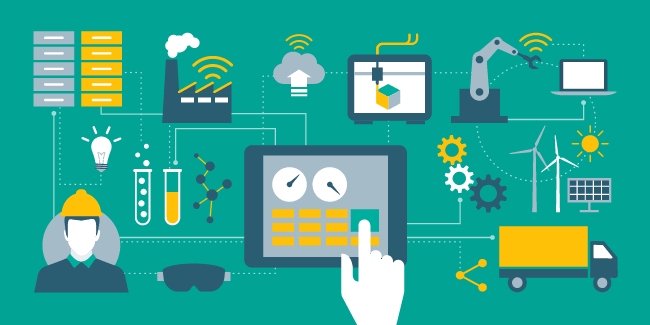
Manufacturing strategy allows businesses to identify their unique selling points and concentrate on them. It is important to establish a competitive edge that will allow you to survive for the long term.
Your manufacturing strategy should match your business goals and mission statement. The strategy should be supported by a strong team leader. This will ensure the allocation of resources to the correct projects, and that everyone knows their part in the company’s success.
Your team will need to discuss and divide the key areas needed for your manufacturing strategy. After they have completed this task, you can create a plan to address each of the key areas.
To increase your employees’ productivity, you can have your team discuss the best ways to improve both the quality and the efficiency of the work they do. It is important to improve the performance of employees as this will result in a more productive working environment and a happier workforce.
In the same vein, you can also look at your overall production capacity and determine if it is adequate for the current and future needs of your business. If not, you may need to invest in more equipment or a new location.
No matter what kind of product you manufacture, it is important that your production be cost-effective. It is crucial to reduce waste and meet customer demands.
Inventory management is one of the best ways to improve production processes. A stock tracking system will help you identify inventory levels that require adjustment. This will make sure that you don't overstock your inventory and end up having many unsold items.
Make-to-order is another way to reduce stock. This is especially useful for businesses who offer niche products which aren't readily available on the high-street.
You can produce finished products when they are needed rather than waiting to receive orders. This will reduce your costs and inventory by a great deal.
Assembling your products is another option. By doing so, you avoid the wasteful use of labour and materials that come with manufacturing large volumes. This is an excellent manufacturing strategy for businesses that want their production process to be as simple and efficient, while still providing a range of products to their customers.
The key to implementing this strategy is having a clear understanding of the products that you are producing and how you intend to manufacture them. It is important to understand your products and how you intend to manufacture them, especially if they are unique or you work in an industry that has complex specifications.
FAQ
How does manufacturing avoid bottlenecks in production?
To avoid production bottlenecks, ensure that all processes run smoothly from the moment you receive your order to the time the product ships.
This includes planning for both capacity requirements and quality control measures.
Continuous improvement techniques like Six Sigma are the best way to achieve this.
Six Sigma can be used to improve the quality and decrease waste in all areas of your company.
It is focused on creating consistency and eliminating variation in your work.
What does warehouse mean?
A warehouse, or storage facility, is where goods are stored prior to being sold. It can be indoors or out. In some cases, it may be a combination of both.
What makes a production planner different from a project manger?
A production planner is more involved in the planning phase of the project than a project manger.
Statistics
- You can multiply the result by 100 to get the total percent of monthly overhead. (investopedia.com)
- In the United States, for example, manufacturing makes up 15% of the economic output. (twi-global.com)
- (2:04) MTO is a production technique wherein products are customized according to customer specifications, and production only starts after an order is received. (oracle.com)
- [54][55] These are the top 50 countries by the total value of manufacturing output in US dollars for its noted year according to World Bank.[56] (en.wikipedia.org)
- According to a Statista study, U.S. businesses spent $1.63 trillion on logistics in 2019, moving goods from origin to end user through various supply chain network segments. (netsuite.com)
External Links
How To
How to Use the Just-In-Time Method in Production
Just-in time (JIT), is a process that reduces costs and increases efficiency in business operations. This is where you have the right resources at the right time. This means that only what you use is charged to your account. The term was first coined by Frederick Taylor, who developed his theory while working as a foreman in the early 1900s. He noticed that workers were often paid overtime when they had to work late. He then concluded that if he could ensure that workers had enough time to do their job before starting to work, this would improve productivity.
JIT is an acronym that means you need to plan ahead so you don’t waste your money. Look at your entire project, from start to end. Make sure you have enough resources in place to deal with any unexpected problems. If you anticipate that there might be problems, you'll have enough people and equipment to fix them. This will prevent you from spending extra money on unnecessary things.
There are different types of JIT methods:
-
Demand-driven: This type of JIT allows you to order the parts/materials required for your project on a regular basis. This will let you track the amount of material left over after you've used it. You'll also be able to estimate how long it will take to produce more.
-
Inventory-based : You can stock the materials you need in advance. This allows for you to anticipate how much you can sell.
-
Project-driven: This method allows you to set aside enough funds for your project. Once you have an idea of how much material you will need, you can purchase the necessary materials.
-
Resource-based JIT: This type of JIT is most commonly used. This is where you assign resources based upon demand. You might assign more people to help with orders if there are many. If there aren't many orders, you will assign fewer people.
-
Cost-based: This is a similar approach to resource-based but you are not only concerned with how many people you have, but also how much each one costs.
-
Price-based pricing: This is similar in concept to cost-based but instead you look at how much each worker costs, it looks at the overall company's price.
-
Material-based: This is very similar to cost-based but instead of looking at total costs of the company you are concerned with how many raw materials you use on an average.
-
Time-based: This is another variation of resource-based JIT. Instead of focusing on the cost of each employee, you will focus on the time it takes to complete a project.
-
Quality-based: This is yet another variation of resource-based JIT. Instead of worrying about the costs of each employee or how long it takes for something to be made, you should think about how quality your product is.
-
Value-based JIT: This is the latest form of JIT. In this instance, you are not concerned about the product's performance or meeting customer expectations. Instead, you're focused on how much value you add to the market.
-
Stock-based is an inventory-based system that measures the number of items produced at any given moment. This method is useful when you want to increase production while decreasing inventory.
-
Just-intime planning (JIT), is a combination JIT/sales chain management. It refers to the process of scheduling the delivery of components as soon as they are ordered. This is important as it reduces lead time and increases throughput.