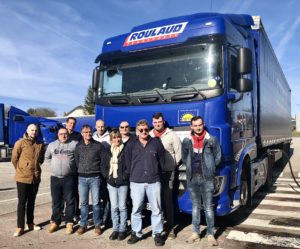
There are many articles about supply chain management. The question is: Which ones are the most cited? This is not an easy question to answer since the topic is awash in academic research. The cocitation analysis is a way to narrow the field. We used the cocitation of the Supply Chain Management Association database to uncover the most frequently cited articles in supply chain management. The International Journal of Supply Chain Management was the top-ranked journal with 25,476 citations. These citations have been grouped into five categories according to their most frequently cited article. Because International Journal of Supply Chain Management is more cited than most journals, it's difficult to predict which order the citations will appear.
Amazon's supply chain practices are the most widely cited article and the one that best reflects the research. Amazon is a company that connects buyers and sellers. The review aims to uncover what works and what doesn't. This article discusses Amazon's various pitfalls as well as its opportunities, and offers some actionable solutions.
A cross-sectional study on supply chain risks and the resulting performance is the most frequently cited article. The study uses both panel and regression data to evaluate the effects of supply-related risks on performance. This is no easy task. These results are stunning. Particularly, the study shows that supply-chain risk management is the best option to improve long-term performance. This has implications for other areas of corporate life, such as procurement and customer service.
Not only is the most-cited article of the same quality, but so are other notable achievements. It is not surprising that the journal with the highest citations has the most publications in the Supply Chain Management Association's database. The International Journal of Supply Chain Management, the Supply Chain Management Association's flagship journal, also has the highest citation count, with 25,476 citations. This is more than double the tally of the Supply Chain Management Association's sister journal, the International Journal of Logistics Research and Applications.
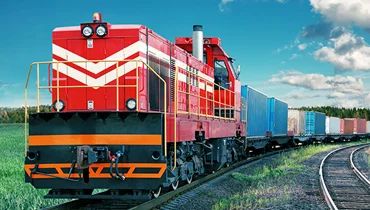
FAQ
What does warehouse refer to?
A warehouse is a place where goods are stored until they are sold. It can be indoors or out. It could be one or both.
What is the role of a manager in manufacturing?
A manufacturing manager has to ensure that all manufacturing processes work efficiently and effectively. They should be aware of any issues within the company and respond accordingly.
They should also learn how to communicate effectively with other departments, including sales and marketing.
They should be up to date on the latest trends and be able apply this knowledge to increase productivity and efficiency.
What are the 7 Rs of logistics.
The acronym "7R's" of Logistics stands for seven principles that underpin logistics management. It was developed and published by the International Association of Business Logisticians in 2004 as part of the "Seven Principles of Logistics Management".
The following letters form the acronym:
-
Responsive - ensure all actions are legal and not harmful to others.
-
Reliable - have confidence in the ability to deliver on commitments made.
-
Reasonable - use resources efficiently and don't waste them.
-
Realistic - Consider all aspects of operations, including environmental impact and cost effectiveness.
-
Respectful - Treat people fairly and equitably
-
Be resourceful: Look for opportunities to save money or increase productivity.
-
Recognizable is a company that provides customers with value-added solutions.
Statistics
- According to the United Nations Industrial Development Organization (UNIDO), China is the top manufacturer worldwide by 2019 output, producing 28.7% of the total global manufacturing output, followed by the United States, Japan, Germany, and India.[52][53] (en.wikipedia.org)
- In 2021, an estimated 12.1 million Americans work in the manufacturing sector.6 (investopedia.com)
- According to a Statista study, U.S. businesses spent $1.63 trillion on logistics in 2019, moving goods from origin to end user through various supply chain network segments. (netsuite.com)
- Many factories witnessed a 30% increase in output due to the shift to electric motors. (en.wikipedia.org)
- [54][55] These are the top 50 countries by the total value of manufacturing output in US dollars for its noted year according to World Bank.[56] (en.wikipedia.org)
External Links
How To
Six Sigma: How to Use it in Manufacturing
Six Sigma is defined by "the application SPC (statistical process control) techniques to achieve continuous improvements." Motorola's Quality Improvement Department created Six Sigma at their Tokyo plant, Japan in 1986. Six Sigma's main goal is to improve process quality by standardizing processes and eliminating defects. Many companies have adopted Six Sigma in recent years because they believe that there are no perfect products and services. Six Sigma aims to reduce variation in the production's mean value. This means that you can take a sample from your product and then compare its performance to the average to find out how often the process differs from the norm. If there is a significant deviation from the norm, you will know that something needs to change.
Understanding how variability works in your company is the first step to Six Sigma. Once you've understood that, you'll want to identify sources of variation. You'll also want to determine whether these variations are random or systematic. Random variations happen when people make errors; systematic variations are caused externally. For example, if you're making widgets, and some of them fall off the assembly line, those would be considered random variations. However, if you notice that every time you assemble a widget, it always falls apart at exactly the same place, then that would be a systematic problem.
Once you have identified the problem, you can design solutions. You might need to change the way you work or completely redesign the process. After implementing the new changes, you should test them again to see if they worked. If they didn't work, then you'll need to go back to the drawing board and come up with another plan.