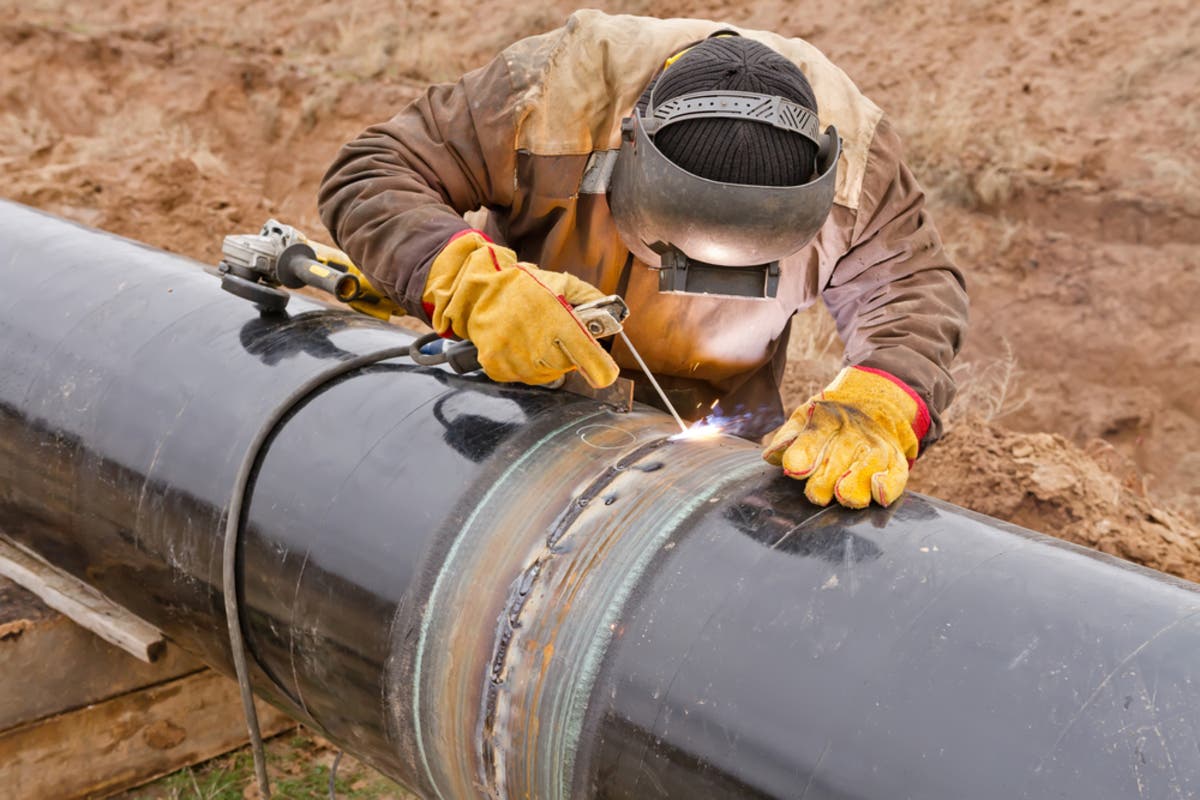
The biggest steel companies in the USA have played a vital role in the economic development of America. They provide vital metals and fabricated products that are used in construction projects, vehicles, homes, and industrial plants. These companies produce a variety metal fabrication services like cutting, bending, stamping, welding, and gallvanizing.
Steel companies in the USA: The biggest steel producers
Steel industry size is affected by many factors. These include raw materials prices, availability of raw materials and the number of smelting facilities and casting plants. The top US-based steel producers produce a total annual output of more than 85 million tons.
Nucor (X) has the most shipments outside of the US. It shipped 3.6M tons of steel during Q3 2019. This is down from the 3.9M tons it shipped in the same quarter in 2018.
The company is large and highly-integrated, and has operations in many industries, including steel, mining and petroleum. It is also the majority owner of a coal-fired plant. This makes it a major player in the energy sector.
Commercial Metals Corporation (CMC) was the third-largest manufacturer of steel, based on shipments. The company shipped 2.1million tons of steel during Q4-2018. The company is vertically-integrated and also manufactures and distributes stainless steel, expanded metal, aluminum and other alloys.
The company has been making a large investment in its iron ore mines in the Great Lakes region and is investing in additional EAFs at existing mills, as well as expanding capacity for flat-rolls at its Baytown, Texas, plate and pipe mill. It also plans a second phase of expansion at its Ohio Flat-Roll mill.
It is one of the few diversified steelmakers, and its main operations are in the United States and Europe. It is also one of the largest producers of high-performance, specialty steels. This includes advanced corrosion resistant and noncorrosive grades.
ArcelorMittal is another major player in the global steel industry. It produces over half the world's total steel. It operates plants in the United States, Canada, Brazil, and Europe and serves markets around the globe. The company's global reach gives it a competitive edge in a market that is becoming more competitive.
China is the biggest producer of steel on earth, and it produces over two-thirds. It has a history of innovation when it comes to steel production.
Although cyclical, this industry is crucial to the growth of the US economy. Construction projects will be needed to replace an aging infrastructure. Demand for new roads, buildings, bridges and other structures is high.
The federal government's $1.2 billion infrastructure spending bill, passed in 2020, is a major driver of the US steel industry. This will be the largest construction in US history, and it will help to boost the economy at home and create jobs. It is estimated that the project will boost the US GDP by $1.3 billion in 2021 and increase demand for steel.
FAQ
How can overproduction in manufacturing be reduced?
Improved inventory management is the key to reducing overproduction. This would reduce the amount of time spent on unnecessary activities such as purchasing, storing, and maintaining excess stock. This could help us free up our time for other productive tasks.
Kanban systems are one way to achieve this. A Kanbanboard is a visual tool that allows you to keep track of the work being done. Kanban systems are where work items travel through a series of states until reaching their final destination. Each state represents a different priority level.
As an example, if work is progressing from one stage of the process to another, then the current task is complete and can be transferred to the next. It is possible to keep a task in the beginning stages until it gets to the end.
This keeps work moving and ensures no work is lost. Managers can see how much work has been done and the status of each task at any time with a Kanban Board. This information allows managers to adjust their workflow based off real-time data.
Lean manufacturing is another option to control inventory levels. Lean manufacturing emphasizes eliminating waste in all phases of production. Waste includes anything that does not add value to the product. Here are some examples of common types.
-
Overproduction
-
Inventory
-
Unnecessary packaging
-
Exceed materials
These ideas will help manufacturers increase efficiency and lower costs.
What are the 7 Rs of logistics management?
The acronym "7R's" of Logistics stands for seven principles that underpin logistics management. It was developed by International Association of Business Logisticians (IABL), and published as part of their "Seven Principles of Logistics Management Series" in 2004.
The acronym is made up of the following letters:
-
Responsible - to ensure that all actions are within the legal requirements and are not detrimental to others.
-
Reliable - Have confidence in your ability to fulfill all of your commitments.
-
Be responsible - Use resources efficiently and avoid wasting them.
-
Realistic - Take into consideration all aspects of operations including cost-effectiveness, environmental impact, and other factors.
-
Respectful: Treat others with fairness and equity
-
Resourceful - look for opportunities to save money and increase productivity.
-
Recognizable - provide customers with value-added services.
What is the responsibility of a production planner?
Production planners make sure that every aspect of the project is delivered on-time, within budget, and within schedule. They also ensure that the product/service meets the client’s needs.
Statistics
- Job #1 is delivering the ordered product according to specifications: color, size, brand, and quantity. (netsuite.com)
- It's estimated that 10.8% of the U.S. GDP in 2020 was contributed to manufacturing. (investopedia.com)
- [54][55] These are the top 50 countries by the total value of manufacturing output in US dollars for its noted year according to World Bank.[56] (en.wikipedia.org)
- (2:04) MTO is a production technique wherein products are customized according to customer specifications, and production only starts after an order is received. (oracle.com)
- According to the United Nations Industrial Development Organization (UNIDO), China is the top manufacturer worldwide by 2019 output, producing 28.7% of the total global manufacturing output, followed by the United States, Japan, Germany, and India.[52][53] (en.wikipedia.org)
External Links
How To
How to use the Just In-Time Production Method
Just-intime (JIT), which is a method to minimize costs and maximize efficiency in business process, is one way. It's a way to ensure that you get the right resources at just the right time. This means that you only pay the amount you actually use. Frederick Taylor developed the concept while working as foreman in early 1900s. After observing how workers were paid overtime for late work, he realized that overtime was a common practice. He decided that workers would be more productive if they had enough time to complete their work before they started to work.
The idea behind JIT is that you should plan ahead and have everything ready so you don't waste money. You should also look at the entire project from start to finish and make sure that you have sufficient resources available to deal with any problems that arise during the course of your project. If you anticipate that there might be problems, you'll have enough people and equipment to fix them. This will prevent you from spending extra money on unnecessary things.
There are several types of JIT techniques:
-
Demand-driven JIT: You order the parts and materials you need for your project every other day. This will allow to track how much material has been used up. This will allow to you estimate the time it will take for more to be produced.
-
Inventory-based : You can stock the materials you need in advance. This allows one to predict how much they will sell.
-
Project-driven : This is a method where you make sure that enough money is set aside to pay the project's cost. Knowing how much money you have available will help you purchase the correct amount of materials.
-
Resource-based JIT: This type of JIT is most commonly used. You allocate resources based on the demand. If you have many orders, you will assign more people to manage them. If you don’t have many orders you will assign less people to the work.
-
Cost-based: This is a similar approach to resource-based but you are not only concerned with how many people you have, but also how much each one costs.
-
Price-based pricing: This is similar in concept to cost-based but instead you look at how much each worker costs, it looks at the overall company's price.
-
Material-based: This is quite similar to cost-based, but instead of looking at the total cost of the company, you're concerned with how much raw materials you spend on average.
-
Time-based JIT: This is another variant of resource-based JIT. Instead of focusing on the cost of each employee, you will focus on the time it takes to complete a project.
-
Quality-based JIT is another variant of resource-based JIT. Instead of focusing on the cost of each worker or how long it takes, think about how high quality your product is.
-
Value-based: This is one of the newest forms of JIT. In this case, you're not concerned with how well the products perform or whether they meet customer expectations. Instead, you are focused on adding value to the marketplace.
-
Stock-based is an inventory-based system that measures the number of items produced at any given moment. This method is useful when you want to increase production while decreasing inventory.
-
Just-intime (JIT), planning is a combination JIT management and supply chain management. It's the process of scheduling delivery of components immediately after they are ordered. This is important as it reduces lead time and increases throughput.