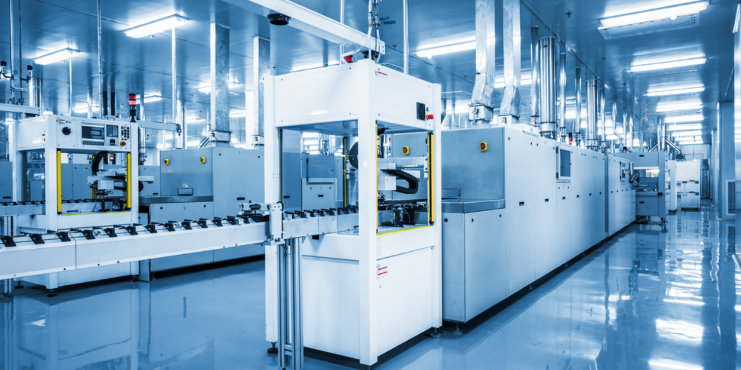
Having an effective supply chain can have a positive impact on all aspects of a company. Customers will be satisfied, costs will drop and the company's growth will increase. No matter how big or small your business is, your supply chain will be a major factor in its success.
The supply chain can be the area that is most often ignored by a business, yet it has the greatest impact on its overall performance and return on investment. If your supply chain is organized, there will be fewer delays and fewer costly material shortages.
Successful supply chain management also improves consumer satisfaction by delivering the right product and quantity at the right time. It increases profits and boosts your company's reputation.
Companies have been trying to achieve greater speed and lower costs in the supply chain for a long time. They have heavily invested into new technology, infrastructure and process.
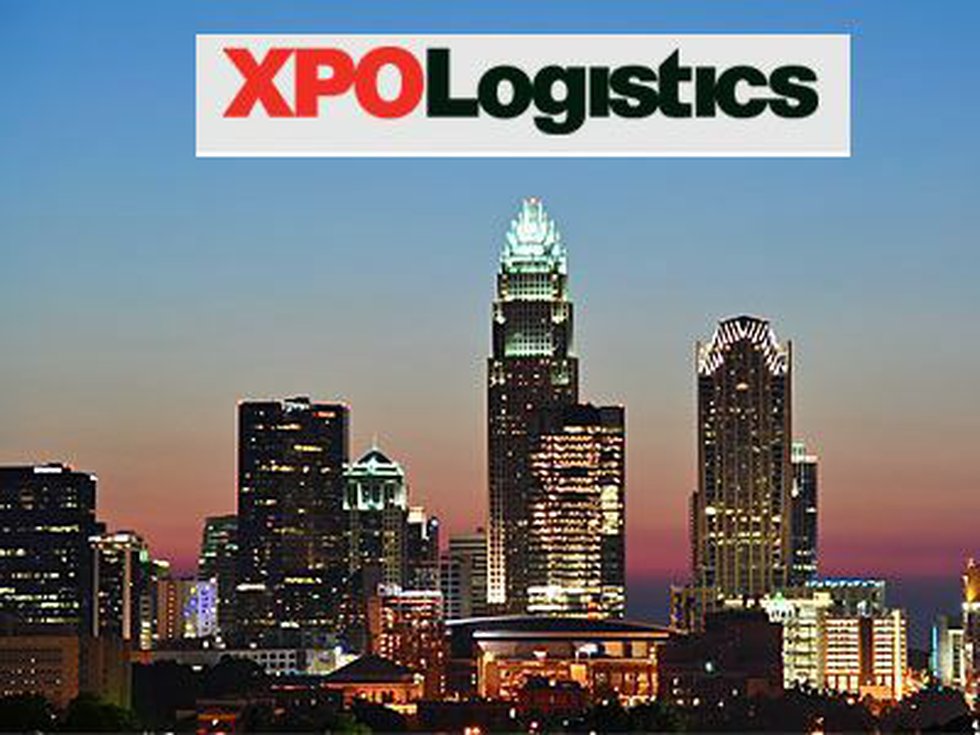
A number of studies show that a firm’s supply chain capabilities can have a profound effect on its financial and operational performance. They are responsible for determining how well the business is run and whether it can meet its customers' requirements.
The supply chain manager who is well trained, and has a thorough understanding of the entire business process can make the necessary trade-offs to save money. They can increase profit, improve customer service and build better relationships with suppliers by working closely together throughout the entire supply chain.
In a world of short product cycles and fast-moving markets, being able to adapt quickly is crucial. It means analyzing and managing raw inventory, transit times, and supplier lead times in real time. The numbers must be accurate, granular and meaningful.
Supply chain managers should understand the impact of a single missed shipment on the bottom-line. In addition, they must be able to plan for backup supplies.
These backup plans can help them overcome unexpected challenges. They will also give them a competitive advantage over their rivals that lack flexible supply chains.
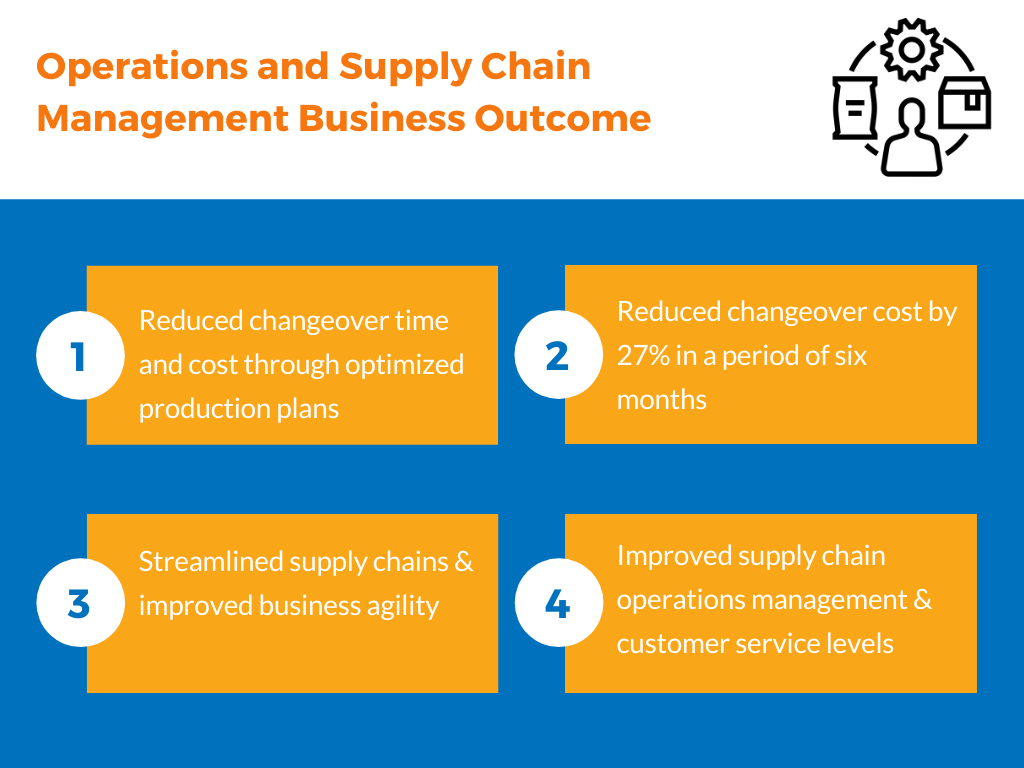
The most important part of any successful business is a well-organized supply chain. This ensures that the correct products are delivered to consumers at the right time, which fulfills their requirements and increases their loyalty.
Consideration of the different stages a product goes through during its life cycle is crucial when aligning your supply system with the manufacturing and distribution systems. This will enable you to design optimal supply-chain solutions that are tailored to the specific needs of each type of product and its stage in life.
A good supply-chain strategy will make sure that the organisation is "fit for purpose" and can change from being flexible and responsive to efficient, low-cost and innovation driven.
To support the business strategy, the organizational design of supply chain functions interacts assets, technologies, processes and employees. When these elements are not aligned, execution can be challenging and a company's supply chain may fail to deliver on its promises.
FAQ
What is the difference between manufacturing and logistics
Manufacturing is the production of goods using raw materials. Logistics encompasses the management of all aspects associated with supply chain activities such as procurement, production planning, distribution and inventory control. It also includes customer service. Manufacturing and logistics can often be grouped together to describe a larger term that covers both the creation of products, and the delivery of them to customers.
What skills is required for a production planner?
Being a production planner is not easy. You need to be organized and flexible. You must also be able to communicate effectively with clients and colleagues.
How can overproduction in manufacturing be reduced?
Better inventory management is key to reducing excess production. This would reduce time spent on activities such as purchasing, stocking, and maintaining excess stock. We could use these resources to do other productive tasks.
One way to do this is to adopt a Kanban system. A Kanban board can be used to monitor work progress. In a Kanban system, work items move through a sequence of states until they reach their final destination. Each state represents a different priority level.
When work is completed, it can be transferred to the next stage. However, if a task is still at the beginning stages, it will remain so until it reaches the end of the process.
This allows for work to continue moving forward, while also ensuring that there is no work left behind. Managers can view the Kanban board to see how much work they have done. This information allows them to adjust their workflow based on real-time data.
Lean manufacturing can also be used to reduce inventory levels. Lean manufacturing emphasizes eliminating waste in all phases of production. Anything that does nothing to add value to a product is waste. Here are some examples of common types.
-
Overproduction
-
Inventory
-
Packaging that is not necessary
-
Excess materials
These ideas can help manufacturers improve efficiency and reduce costs.
What are the 7 Rs of logistics?
The acronym 7Rs of Logistics refers to the seven core principles of logistics management. It was published in 2004 by the International Association of Business Logisticians as part of their "Seven Principles of Logistics Management" series.
The acronym is made up of the following letters:
-
Responsible - to ensure that all actions are within the legal requirements and are not detrimental to others.
-
Reliable – have faith in your ability and capability to keep promises.
-
It is reasonable to use resources efficiently and not waste them.
-
Realistic - Take into consideration all aspects of operations including cost-effectiveness, environmental impact, and other factors.
-
Respectful: Treat others with fairness and equity
-
Responsive - Look for ways to save time and increase productivity.
-
Recognizable - Provide value-added services to customers
Statistics
- According to the United Nations Industrial Development Organization (UNIDO), China is the top manufacturer worldwide by 2019 output, producing 28.7% of the total global manufacturing output, followed by the United States, Japan, Germany, and India.[52][53] (en.wikipedia.org)
- Job #1 is delivering the ordered product according to specifications: color, size, brand, and quantity. (netsuite.com)
- In 2021, an estimated 12.1 million Americans work in the manufacturing sector.6 (investopedia.com)
- It's estimated that 10.8% of the U.S. GDP in 2020 was contributed to manufacturing. (investopedia.com)
- According to a Statista study, U.S. businesses spent $1.63 trillion on logistics in 2019, moving goods from origin to end user through various supply chain network segments. (netsuite.com)
External Links
How To
How to use 5S in Manufacturing to Increase Productivity
5S stands for "Sort", "Set In Order", "Standardize", "Separate" and "Store". Toyota Motor Corporation was the first to develop the 5S approach in 1954. It improves the work environment and helps companies to achieve greater efficiency.
This approach aims to standardize production procedures, making them predictable, repeatable, and easily measurable. This means that every day tasks such cleaning, sorting/storing, packing, and labeling can be performed. Workers can be more productive by knowing what to expect.
There are five steps that you need to follow in order to implement 5S. Each step is a different action that leads to greater efficiency. By sorting, for example, you make it easy to find the items later. When you arrange items, you place them together. After you have divided your inventory into groups you can store them in easy-to-reach containers. You can also label your containers to ensure everything is properly labeled.
Employees must be able to critically examine their work practices. Employees need to understand the reasons they do certain jobs and determine if there is a better way. In order to use the 5S system effectively, they must be able to learn new skills.
The 5S Method not only improves efficiency, but it also helps employees to be more productive and happier. Once they start to notice improvements, they are motivated to keep working towards their goal of increasing efficiency.