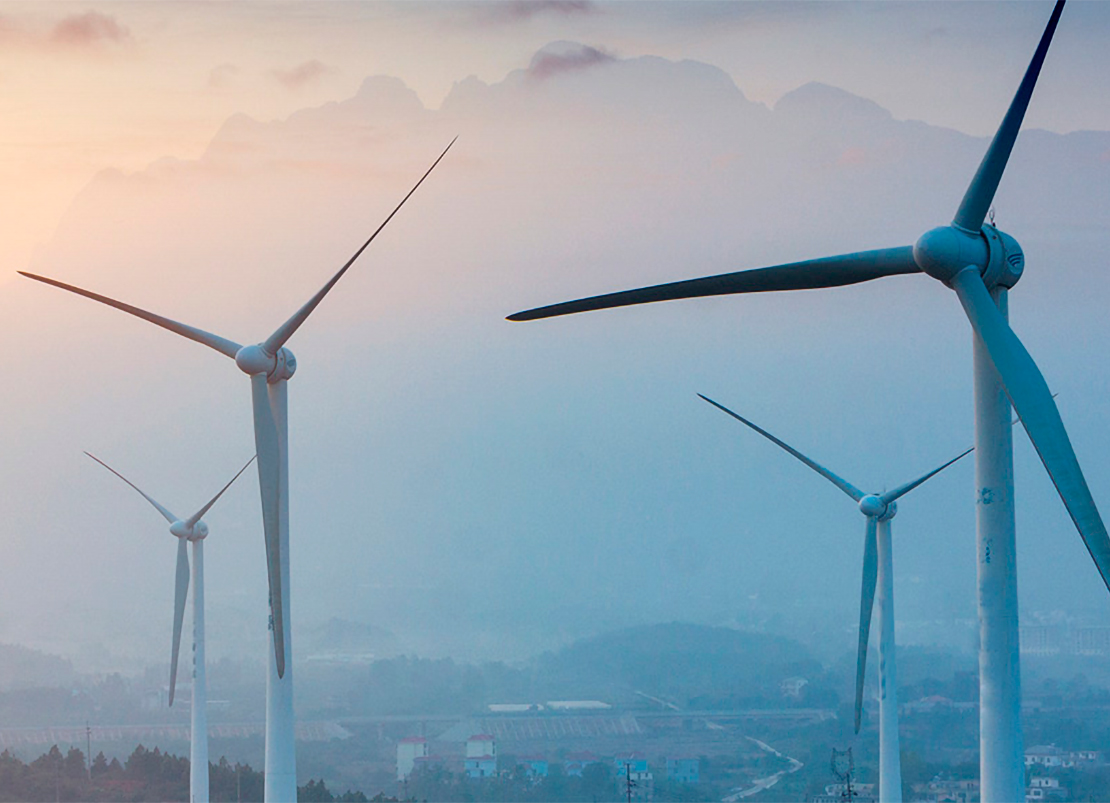
Although lean manufacturing offers many advantages, some companies have had difficulties implementing this strategy. Companies must develop a plan to overcome these challenges. Companies that have implemented Lean know that there are three key issues that hinder its success.
A commitment to lean manufacturing, regardless of how big a company might be, is vital to its success. Although there are no easy ways to measure how committed a company has been to lean manufacturing implementations, it is crucial that staff are familiarized with the changes and culture.
It is also important to ensure that resources are allocated correctly. Public organizations often find that they spend their budgets on unnecessary items. Some managers have also been reported to purchase equipment that is not needed in order to use the budget. This can lead to operational bottlenecks and inefficient implementation of lean manufacturing.
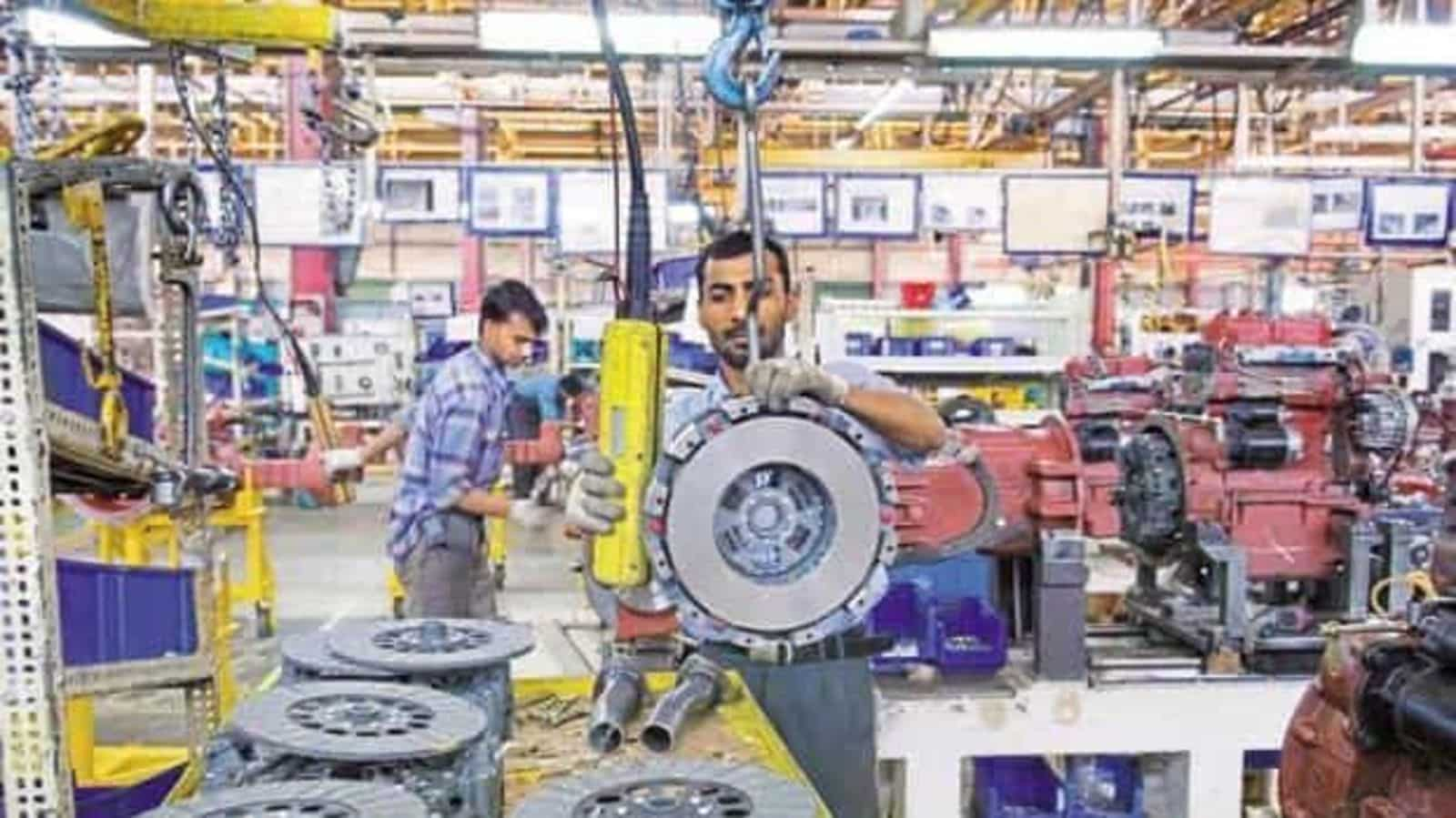
One of the biggest challenges in implementing lean manufacturing is resistance to cultural change. Many employees, especially those that have been with the company for a long time, are not comfortable with change. These employees might wait for the majority of the workforce to convince them to change. Management must explain the benefits of the program to employees and why they are necessary for the change to be successful.
Another significant challenge is the lack of a strategic transformation plan. Although companies often manage multiple business operations at once it is essential to develop a long-term strategy. This strategy allows companies mentor future leaders and keeps them competitive in the face technology advances. It also helps to improve operational efficiency. It also helps identify and address operational bottlenecks and identify and address growth opportunities.
It is vital to train workers to overcome resistance. The proper training helps workers understand their responsibilities and expectations. The training also helps workers to develop multi-skills, which can be used to do more work independently. Worker training also aids in problem solving, which allows them to maintain Lean through increased performance.
Management needs to be open and honest with employees in order for them to overcome resistance. Managers might use pressure to get workers into compliance, but managers should also be willing to explain why this change is necessary. Sometimes, managers gave incorrect instructions to workers, leading to ineffective implementation.
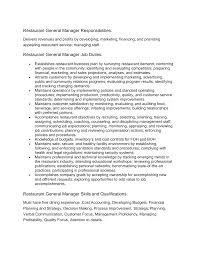
Regardless of the size of he company, managers must be involved on the shop floor, allowing them to identify the areas where changes can be made. They must also create and train staff using digital tools. These tools, including 5S (visual management), improve visual management.
It is vital to create and communicate a clear vision regarding the implementation of lean manufacturing. This vision should contain information about employees' responsibilities, the schedule for lean implementation, and how to measure success.
FAQ
Why is logistics so important in manufacturing?
Logistics are an integral part any business. They help you achieve great results by helping you manage all aspects of product flow, from raw materials to finished goods.
Logistics also play a major role in reducing costs and increasing efficiency.
What is it like to manage a logistics company?
To be a successful businessman in logistics, you will need many skills and knowledge. You must have good communication skills to interact effectively with your clients and suppliers. You need to understand how to analyze data and draw conclusions from it. You will need to be able handle pressure well and work in stressful situations. To increase efficiency and creativity, you need to be creative. To motivate and guide your team towards reaching organizational goals, you must have strong leadership skills.
To meet tight deadlines, you must also be efficient and organized.
How can I find out more about manufacturing?
Hands-on experience is the best way to learn more about manufacturing. If that is not possible, you could always read books or view educational videos.
What does it mean to warehouse?
A warehouse is an area where goods are stored before being sold. It can be indoors or out. In some cases it could be both indoors and outdoors.
What are the 7 Rs of logistics?
The acronym 7Rs of Logistics refers to the seven core principles of logistics management. It was published in 2004 by the International Association of Business Logisticians as part of their "Seven Principles of Logistics Management" series.
The following letters form the acronym:
-
Responsive - ensure all actions are legal and not harmful to others.
-
Reliable – have faith in your ability and capability to keep promises.
-
Use resources effectively and sparingly.
-
Realistic – Consider all aspects, including cost-effectiveness as well as environmental impact.
-
Respectful - Treat people fairly and equitably
-
Reliable - Find ways to save money and increase your productivity.
-
Recognizable: Provide customers with value-added service
Statistics
- In 2021, an estimated 12.1 million Americans work in the manufacturing sector.6 (investopedia.com)
- You can multiply the result by 100 to get the total percent of monthly overhead. (investopedia.com)
- It's estimated that 10.8% of the U.S. GDP in 2020 was contributed to manufacturing. (investopedia.com)
- In the United States, for example, manufacturing makes up 15% of the economic output. (twi-global.com)
- According to a Statista study, U.S. businesses spent $1.63 trillion on logistics in 2019, moving goods from origin to end user through various supply chain network segments. (netsuite.com)
External Links
How To
How to use the Just In-Time Production Method
Just-in-time is a way to cut costs and increase efficiency in business processes. It's the process of obtaining the right amount and timing of resources when you need them. This means that your only pay for the resources you actually use. Frederick Taylor first coined this term while working in the early 1900s as a foreman. Taylor observed that overtime was paid to workers if they were late in working. He decided to ensure workers have enough time to do their jobs before starting work to improve productivity.
JIT is an acronym that means you need to plan ahead so you don’t waste your money. Look at your entire project, from start to end. Make sure you have enough resources in place to deal with any unexpected problems. If you expect problems to arise, you will be able to provide the necessary equipment and personnel to address them. This way, you won't end up paying extra money for things that weren't really necessary.
There are many types of JIT methods.
-
Demand-driven JIT: You order the parts and materials you need for your project every other day. This will let you track the amount of material left over after you've used it. This will let you know how long it will be to produce more.
-
Inventory-based : You can stock the materials you need in advance. This allows you predict the amount you can expect to sell.
-
Project-driven: This approach involves setting aside sufficient funds to cover your project's costs. When you know how much you need, you'll purchase the appropriate amount of materials.
-
Resource-based JIT : This is probably the most popular type of JIT. You allocate resources based on the demand. For instance, if you have a lot of orders coming in, you'll assign more people to handle them. You'll have fewer orders if you have fewer.
-
Cost-based: This is the same as resource-based except that you don't care how many people there are but how much each one of them costs.
-
Price-based: This is a variant of cost-based. However, instead of focusing on the individual workers' costs, this looks at the total price of the company.
-
Material-based - This is a variant of cost-based. But instead of looking at the total company cost, you focus on how much raw material you spend per year.
-
Time-based JIT: This is another variant of resource-based JIT. Instead of worrying about how much each worker costs, you can focus on how long the project takes.
-
Quality-based JIT: Another variation on resource-based JIT. Instead of looking at the labor costs and time it takes to make a product, think about its quality.
-
Value-based: This is one of the newest forms of JIT. In this scenario, you're not concerned about how products perform or whether customers expect them to meet their expectations. Instead, you focus on the added value that you provide to your market.
-
Stock-based: This is an inventory-based method that focuses on the actual number of items being produced at any given time. This method is useful when you want to increase production while decreasing inventory.
-
Just-in-time (JIT) planning: This is a combination of JIT and supply chain management. It is the process of scheduling components' delivery as soon as they have been ordered. It is essential because it reduces lead-times and increases throughput.