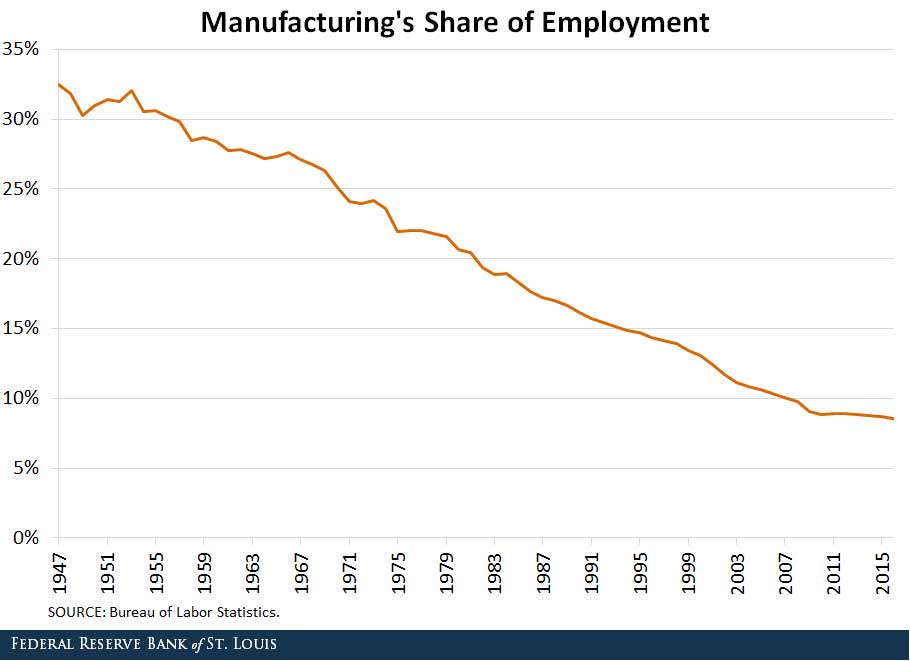
The Industrial Products & Services sector of the industrial manufacturing industry is experiencing increased global competition and a shortage in skilled workers. In 2020, the industry will face a complex landscape due to volatility in supply chains and increased competition. The Industrial Products & Services sector requires a comprehensive culture of innovation to ensure optimisation of growth in established markets, while also optimising for growth opportunities in new markets.
According to the Deloitte and Manufacturing Institute study, the US manufacturing workforce will experience the largest shortfall of skilled workers in history, as 2 million jobs are estimated to be unfilled over the next decade. The future of the industry is now in the hands of manufacturers. They must decide how to develop their digital capabilities and innovate. Deloitte's Industrial Manufacturing team can assist manufacturers in navigating the industry landscape.
The fourth industrial revolution continues to disrupt manufacturing. This means that the industry must prepare its workforce for a future where there will be networking and digital transformation. The Industrial Manufacturing team has extensive experience in creating innovative management models that are grounded on industry-specific knowledge and industry expertise. It offers a broad range of digital transformation services that will help manufacturers succeed in a digitally disrupted world.
The Deloitte report is based on extensive secondary information analysis of labor supply. Interviews with executives from various manufacturing companies are also part of the research. Economic projections are also included. It is important to have a diverse workforce, according to the findings. One of the key factors in job satisfaction was cited by half of the respondents as adaptability to company culture. Over a third of respondents said that employees need to have a purpose to feel satisfied at their jobs. Executives believe that millennials are more aware of the importance and will be more concerned about climate issues.
Using the Oxford Economic Model, Deloitte predicts that manufacturing GDP will grow at a moderate rate of 1.3 percent in 2020. The study does note that this rate of growth will be lower than the previous few years. This means that companies will need to rethink their approaches to supply chain assurance. Companies will also need to concentrate on wider management initiatives, such as improving operational resilience. According to Deloitte's study, manufacturers will be making decisions regarding work environments and work practices.
Manufacturing companies should create opportunities for career advancement and promote inclusion in order to plan for the future. Manufacturing efficiency can be improved and waste reduced by increasing resilience. Combining lean principles and digital technologies can also reduce manufacturing variability.
Deloitte recently released a report that examines diversity within the US manufacturing market. Deloitte’s Beyond Reskilling report discusses diversity and how it is vital for the future of manufacturing. It also highlights benefits of having a diverse workforce.
FAQ
What is the difference in Production Planning and Scheduling, you ask?
Production Planning (PP) refers to the process of determining how much production is needed at any given moment. Forecasting and identifying production capacity are two key elements to this process.
Scheduling involves the assignment of dates and times to tasks in order to complete them within the timeframe.
What is production plan?
Production planning is the process of creating a plan that covers all aspects of production. This includes scheduling, budgeting and crew, location, equipment, props, and more. This document is designed to make sure everything is ready for when you're ready to shoot. You should also have information to ensure the best possible results on set. It should include information about shooting locations, casting lists, crew details, equipment requirements, and shooting schedules.
The first step in filming is to define what you want. You may have decided where to shoot or even specific locations you want to use. Once you have identified your locations and scenes it's time to begin figuring out what elements you will need for each one. You might decide you need a car, but not sure what make or model. You could look online for cars to see what options are available, and then narrow down your choices by selecting between different makes or models.
After you have selected the car you want, you can begin to think about additional features. Are you looking for people to sit in the front seats? You might also need someone to help you get around the back. Perhaps you would like to change the interior colour from black to white. These questions will help to determine the style and feel of your car. You can also think about the type of shots you want to get. Are you going to be shooting close-ups? Or wide angles? Perhaps you want to show the engine or the steering wheel? This will allow you to determine the type of car you want.
Once you have made all the necessary decisions, you can start to create a schedule. You can create a schedule that will outline when you must start and finish your shoots. Every day will have a time for you to arrive at the location, leave when you are leaving and return home when you are done. So everyone is clear about what they need to do. If you need to hire extra staff, you can make sure you book them in advance. You should not hire anyone who doesn't show up because of your inaction.
It is important to calculate the amount of filming days when you are creating your schedule. Some projects only take one or two days, while others may last weeks. When creating your schedule, be aware of whether you need more shots per day. Multiple takes at the same place will result in higher costs and longer completion times. You can't be certain if you will need multiple takes so it is better not to shoot too many.
Another important aspect of production planning is setting budgets. You will be able to manage your resources if you have a realistic budget. Remember that you can always reduce the budget later on if you run into unforeseen problems. But, don't underestimate how much money you'll spend. If you underestimate how much something costs, you'll have less money to pay for other items.
Production planning is a detailed process. But, once you understand the workings of everything, it becomes easier for future projects to be planned.
What are the 7 R's of logistics?
The acronym 7Rs of Logistics refers to the seven core principles of logistics management. It was developed and published by the International Association of Business Logisticians in 2004 as part of the "Seven Principles of Logistics Management".
The acronym is composed of the following letters.
-
Responsible – ensure that all actions are legal and don't cause harm to anyone else.
-
Reliable - have confidence in the ability to deliver on commitments made.
-
Use resources effectively and sparingly.
-
Realistic – Consider all aspects, including cost-effectiveness as well as environmental impact.
-
Respectful - Treat people fairly and equitably
-
Be resourceful: Look for opportunities to save money or increase productivity.
-
Recognizable: Provide customers with value-added service
Can certain manufacturing steps be automated?
Yes! Yes! Automation has existed since ancient times. The Egyptians invented the wheel thousands of years ago. Today, robots assist in the assembly of lines.
There are many applications for robotics in manufacturing today. These include:
-
Automation line robots
-
Robot welding
-
Robot painting
-
Robotics inspection
-
Robots create products
Automation could also be used to improve manufacturing. For example, 3D printing allows us to make custom products without having to wait for weeks or months to get them manufactured.
What is the job of a production plan?
Production planners ensure all aspects of the project are delivered within time and budget. They also ensure that the product/service meets the client’s needs.
How can efficiency in manufacturing be improved?
The first step is to determine the key factors that impact production time. Then we need to find ways to improve these factors. If you don’t know how to start, look at which factors have the greatest impact upon production time. Once you have identified the factors, then try to find solutions.
What are the products of logistics?
Logistics refers to the movement of goods from one place to another.
They cover all aspects of transportation, such as packing, loading, transporting and unloading.
Logisticians ensure that products reach the right destination at the right moment and under safe conditions. Logisticians assist companies in managing their supply chains by providing information such as demand forecasts, stock levels and production schedules.
They can also track shipments in transit and monitor quality standards.
Statistics
- According to the United Nations Industrial Development Organization (UNIDO), China is the top manufacturer worldwide by 2019 output, producing 28.7% of the total global manufacturing output, followed by the United States, Japan, Germany, and India.[52][53] (en.wikipedia.org)
- (2:04) MTO is a production technique wherein products are customized according to customer specifications, and production only starts after an order is received. (oracle.com)
- You can multiply the result by 100 to get the total percent of monthly overhead. (investopedia.com)
- In 2021, an estimated 12.1 million Americans work in the manufacturing sector.6 (investopedia.com)
- It's estimated that 10.8% of the U.S. GDP in 2020 was contributed to manufacturing. (investopedia.com)
External Links
How To
Six Sigma and Manufacturing
Six Sigma can be described as "the use of statistical process control (SPC), techniques to achieve continuous improvement." Motorola's Quality Improvement Department created Six Sigma at their Tokyo plant, Japan in 1986. Six Sigma's main goal is to improve process quality by standardizing processes and eliminating defects. In recent years, many companies have adopted this method because they believe there is no such thing as perfect products or services. The main goal of Six Sigma is to reduce variation from the mean value of production. You can calculate the percentage of deviation from the norm by taking a sample of your product and comparing it to the average. If it is too large, it means that there are problems.
Understanding the dynamics of variability within your business is the first step in Six Sigma. Once you understand this, you can then identify the causes of variation. Also, you will need to identify the sources of variation. Random variations happen when people make errors; systematic variations are caused externally. If you make widgets and some of them end up on the assembly line, then those are considered random variations. But if you notice that every widget you make falls apart at the exact same place each time, this would indicate that there is a problem.
Once you identify the problem areas, it is time to create solutions. That solution might involve changing the way you do things or redesigning the process altogether. To verify that the changes have worked, you need to test them again. If they don’t work, you’ll need to go back and rework the plan.