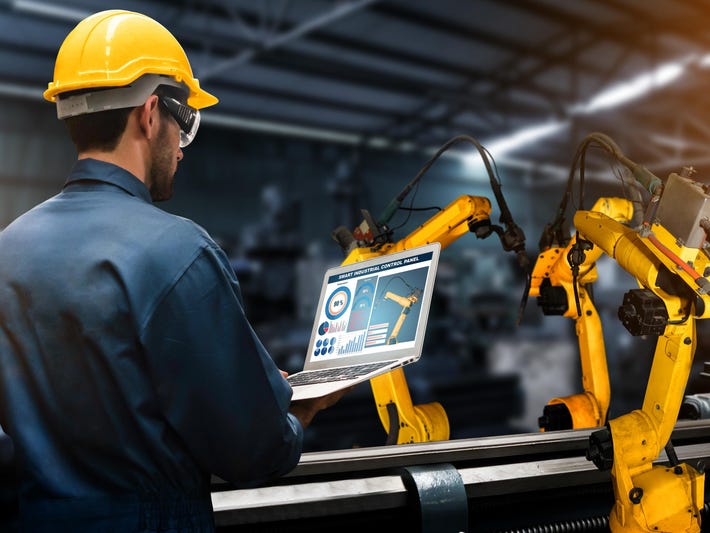
Toyota has always maintained its core goal of making high quality products, regardless of its success. Toyota has been a top-selling automotive brand because of its unwavering dedication to excellence.
Toyota's strategy centers on staying true and focused on incremental innovations. It also promotes smart growth. It also stresses the importance of building and nurturing relationships with its dealers. Toyota puts its customers ahead of other companies, even though they may rely on stock prices. This is because the automobile industry is highly competitive and a company's success depends on its ability to innovate.
Toyota employees must face new challenges to ensure its continued success. Toyota encourages employees, to think outside the box and come up with new ideas. Open communication is encouraged and employees are challenged to reach out beyond differences and compromises. This is accomplished through on-the-job training. Employees are encouraged to share their mistakes and problems.
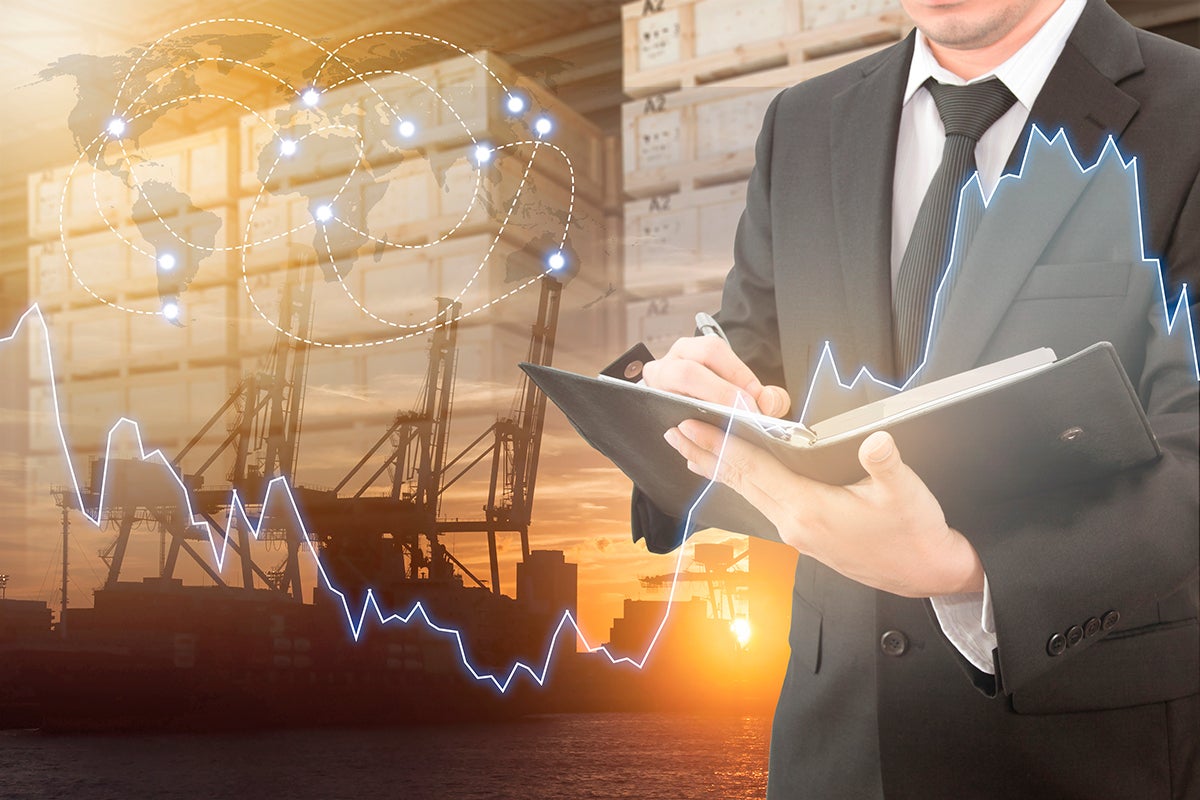
Another way Toyota manages to succeed is through the use of a "continuous improvement" process, called kaizen. It involves streamlining processes and trying out new ideas. This process is also known in Japanese, as genchi.genbutsu. It assists Toyota in achieving its goals. It is also an integral part Toyota's culture. It has been the core of Toyota's success since decades.
Toyota's first major move was to create a research laboratory. Kiichiro Yoyoda, the founder of Toyota, believed that new technologies were essential for maintaining competitiveness in the automobile industry. He created a research laboratory in the late 30s. He envisaged a Japan with its own automobiles, and without any foreign technology.
Toyota made a number of strategic moves in 1950s. It started to diversify its product lines and export cars to foreign countries. It also established a separate sales company and established a network of dealers. It also started to gain an understanding of international automobile markets. It realized that European and American automakers would overwhelm Toyota if it were to compete in the global marketplace.
Toyota's decision to establish a division in America was another major move it made in the 1950s. It was aware that American workers were 9 times more productive than Japanese workers. It realized that fuel-efficient cars were in demand. It had to convince American citizens that Japanese cars were a worthwhile investment. It had to overcome a strike in 1950 that was crippling the company. It had to obtain loans and trim staff.
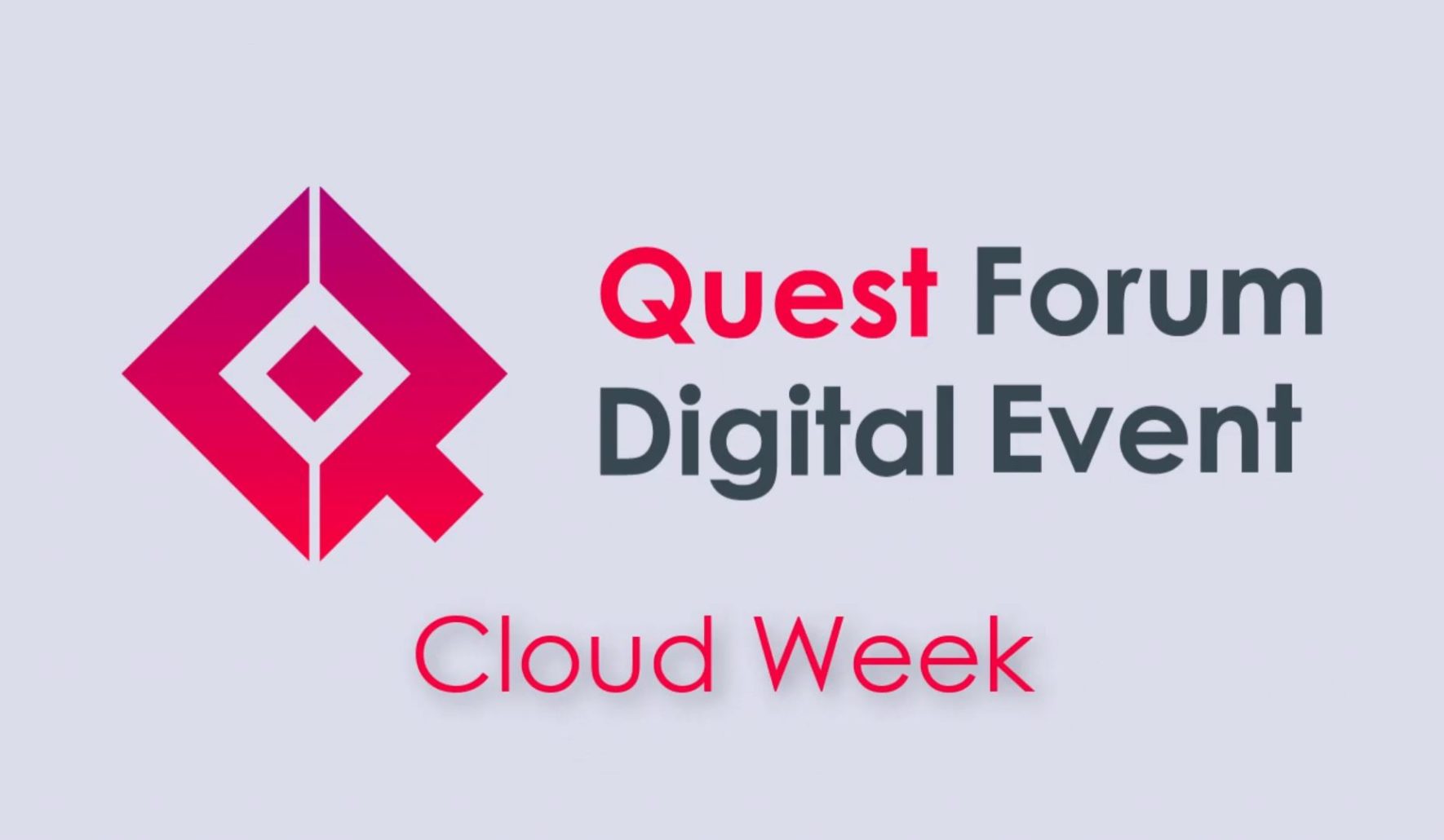
Toyota also established a "driving academy" to help people get their driver's licenses. Toyota also developed a special line of cars for the U.S. market. These initiatives helped to attract consumers into its dealerships.
Toyota's success within the automotive industry is dependent on its ability innovate and create value. It depends also on its ability and willingness to build relationships with suppliers and dealers.
FAQ
What is production planning?
Production Planning refers to the development of a plan for every aspect of production. This document aims to ensure that everything is planned and ready when you are ready to shoot. It should also contain information on achieving the best results on set. This includes shooting schedules, locations, cast lists, crew details, and equipment requirements.
The first step in filming is to define what you want. You may have decided where to shoot or even specific locations you want to use. Once you've identified the locations and scenes you want to use, you can begin to plan what elements you need for each scene. For example, you might decide that you need a car but don't know exactly what model you want. To narrow your options, you can search online for available models.
After you have chosen the right car, you will be able to begin thinking about accessories. You might need to have people in the front seats. Or maybe you just need someone to push the car around. Perhaps you would like to change the interior colour from black to white. These questions will help you determine the exact look and feel of your car. Also, think about what kind of shots you would like to capture. What type of shots will you choose? Perhaps you want to show the engine or the steering wheel? These things will help you to identify the car that you are looking for.
Once you have made all the necessary decisions, you can start to create a schedule. You can create a schedule that will outline when you must start and finish your shoots. Each day will include the time when you need to arrive at the location, when you need to leave and when you need to return home. It will help everyone know exactly what they have to do and when. Hire extra staff by booking them ahead of time. It is not worth hiring someone who won’t show up because you didn’t tell him.
It is important to calculate the amount of filming days when you are creating your schedule. Some projects can be completed in a matter of days or weeks. Others may take several days. While creating your schedule, it is important to remember whether you will require more than one shot per day. Multiple shots at the same location can increase costs and make it more difficult to complete. It's better to be safe than sorry and shoot less takes if you're not certain whether you need more takes.
Budgeting is another important aspect of production planning. You will be able to manage your resources if you have a realistic budget. Keep in mind that you can always reduce your budget if you face unexpected difficulties. However, it is important not to overestimate the amount that you will spend. If you underestimate how much something costs, you'll have less money to pay for other items.
Production planning is a detailed process. But, once you understand the workings of everything, it becomes easier for future projects to be planned.
What are the goods of logistics?
Logistics refers to the movement of goods from one place to another.
They include all aspects associated with transport including packaging, loading transporting, unloading storage, warehousing inventory management customer service, distribution returns and recycling.
Logisticians ensure that the product is delivered to the correct place, at the right time, and under safe conditions. They help companies manage their supply chain efficiency by providing information on demand forecasts, stock levels, production schedules, and availability of raw materials.
They also keep track of shipments in transit, monitor quality standards, perform inventories and order replenishment, coordinate with suppliers and vendors, and provide support services for sales and marketing.
What is the job of a manufacturer manager?
A manufacturing manager must make sure that all manufacturing processes run smoothly and effectively. They should also be aware and responsive to any company problems.
They should also be able and comfortable communicating with other departments like sales and marketing.
They should be up to date on the latest trends and be able apply this knowledge to increase productivity and efficiency.
What are manufacturing & logistics?
Manufacturing is the process of creating goods from raw materials by using machines and processes. Logistics manages all aspects of the supply chain, including procurement, production planning and distribution, inventory control, transportation, customer service, and transport. Manufacturing and logistics can often be grouped together to describe a larger term that covers both the creation of products, and the delivery of them to customers.
Are there any Manufacturing Processes that we should know before we can learn about Logistics?
No. No. Knowing about manufacturing processes will help you understand how logistics works.
What are the 7 R's of logistics?
The 7R's of Logistics is an acronym for the seven basic principles of logistics management. It was developed by the International Association of Business Logisticians (IABL) and published in 2004 as part of its "Seven Principles of Logistics Management" series.
The following letters make up the acronym:
-
Responsible - to ensure that all actions are within the legal requirements and are not detrimental to others.
-
Reliable – have faith in your ability and capability to keep promises.
-
Reasonable - use resources efficiently and don't waste them.
-
Realistic – consider all aspects of operations, from cost-effectiveness to environmental impact.
-
Respectful: Treat others with fairness and equity
-
Resourceful - look for opportunities to save money and increase productivity.
-
Recognizable provides value-added products and services to customers
Statistics
- (2:04) MTO is a production technique wherein products are customized according to customer specifications, and production only starts after an order is received. (oracle.com)
- In the United States, for example, manufacturing makes up 15% of the economic output. (twi-global.com)
- According to a Statista study, U.S. businesses spent $1.63 trillion on logistics in 2019, moving goods from origin to end user through various supply chain network segments. (netsuite.com)
- [54][55] These are the top 50 countries by the total value of manufacturing output in US dollars for its noted year according to World Bank.[56] (en.wikipedia.org)
- In 2021, an estimated 12.1 million Americans work in the manufacturing sector.6 (investopedia.com)
External Links
How To
How to Use the 5S to Increase Productivity In Manufacturing
5S stands to stand for "Sort", “Set In Order", “Standardize", and "Store". Toyota Motor Corporation developed the 5S method in 1954. It assists companies in improving their work environments and achieving higher efficiency.
The idea behind standardizing production processes is to make them repeatable and measurable. This means that daily tasks such as cleaning and sorting, storage, packing, labeling, and packaging are possible. This knowledge allows workers to be more efficient in their work because they are aware of what to expect.
Five steps are required to implement 5S: Sort, Set In Order, Standardize. Separate. Each step is a different action that leads to greater efficiency. If you sort items, it makes them easier to find later. You arrange items by placing them in an order. You then organize your inventory in groups. Finally, when you label your containers, you ensure everything is labeled correctly.
Employees will need to be more critical about their work. Employees must understand why they do certain tasks and decide if there's another way to accomplish them without relying on the old ways of doing things. To implement the 5S system, employees must acquire new skills and techniques.
In addition to increasing efficiency, the 5S method also improves morale and teamwork among employees. They will feel motivated to strive for higher levels of efficiency once they start to see results.