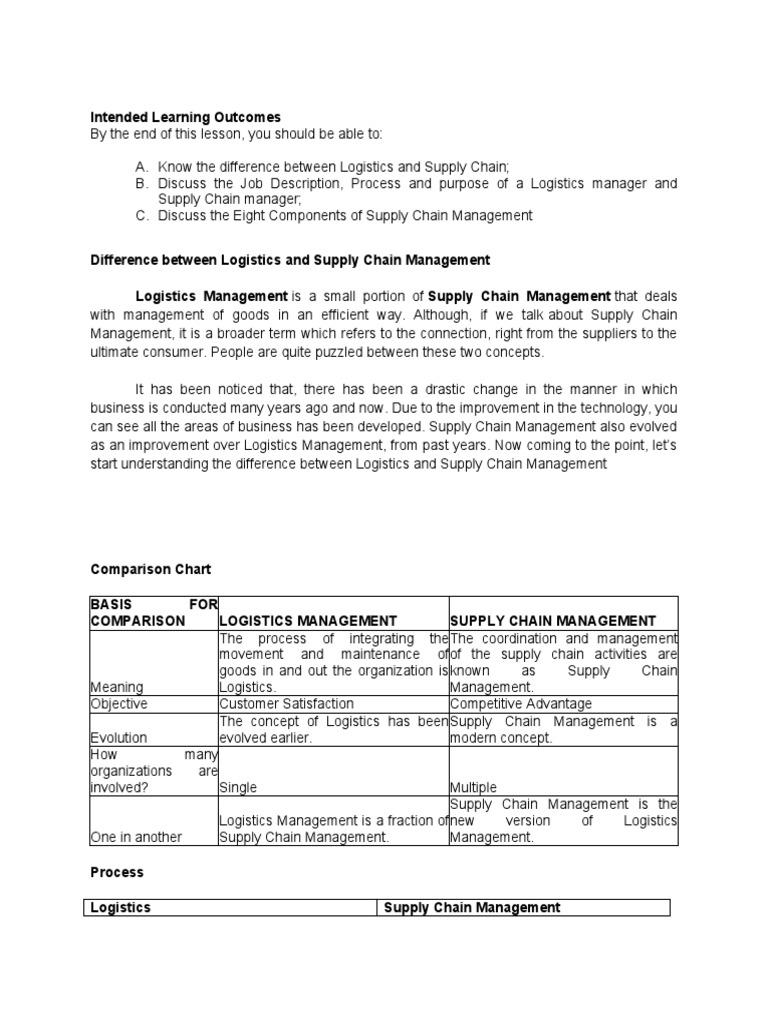
As a study engineer, you use a combination of creativity and scientific analysis to design and create things that improve the world around us. Your work can make a huge difference in the lives of people, whether it's designing bridges or medical equipment, or cleaning up toxic waste.
Engineering is a vast and versatile academic field, so choosing the right course is important. Kingston University has undergraduate degrees available in chemical, mechanical, civil, electrical, and civil engineering.
A bachelor's degree in engineering is the first step to becoming a professional engineer. The curriculum includes math, science, humanities and other courses that are applicable to many careers.
Some engineers choose to earn a Master's or Doctorate degree so that they can specialize in a certain area. They can expand your options for a career and increase your job prospects.
You can also take an industry-specific engineering course, such as mining or oil and gas. These courses teach you about how to assess and explore underground mineral resources.
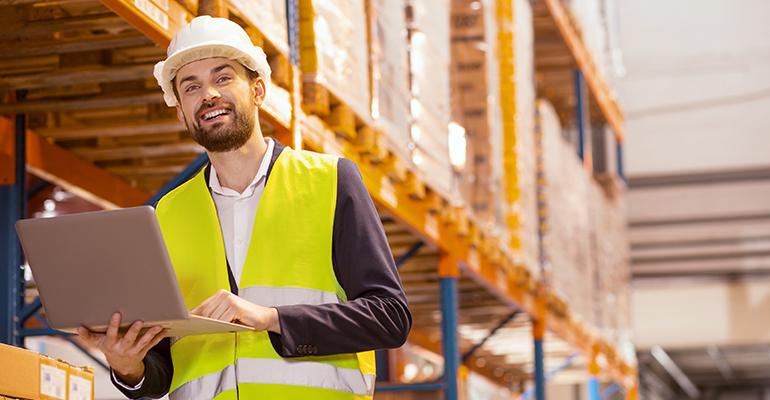
Manufacturing is the process that transforms raw materials into finished goods for sale in markets or stores. You will learn about the basics of production, including how to plan and implement production lines.
As an engineer you will need to be able manage your time and prioritize tasks to complete them within a certain window of time. You will also have to manage time and prioritize so that you can finish your tasks within a set time frame.
If you are pursuing an engineering education, you will need to find a college which offers an accredited program. This means that the institution has met the requirements set by ABET. ABET is the organization responsible for accrediting engineering education in the United States.
You will need to be a full-time student for four years, and complete a minimum 60 credit hours per semester. In addition, you'll need to pass an exam and get a work experience internship in your chosen engineering field.
The average annual pay of a study engineer in the United States is $94,463. This includes an entry-level wage of around $30,000. A senior research engineer earns about $123,325 a year.
As a study engineer, you will be responsible for identifying and evaluating new technologies that can assist companies in producing more efficient and cheaper products. You will also develop designs and test prototypes to ensure their functionality, ease of use and durability. It may also include collaborating with product development and marketing to refine existing products or developing new ones.
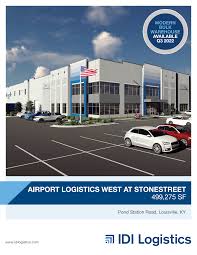
You will need to spend significant time in both the lab and the workplace as a Study Engineer. You'll need to be able to perform complex analyses of data and develop a solid understanding of the science behind your engineering projects.
You should have a passion for science and a desire to solve complex problems if you plan to study engineering. You'll also need to have a background in physics, math and chemistry.
It is best to enroll in an accredited engineering program, and then to take the FE test after graduating. You'll then need to gain some experience in engineering before you take the PE exam.
FAQ
Why automate your factory?
Automation has become increasingly important in modern warehousing. Increased demand for efficient and faster delivery has resulted in a rise in e-commerce.
Warehouses have to be flexible to meet changing requirements. They must invest heavily in technology to do this. The benefits of automating warehouses are numerous. Here are some reasons why it's worth investing in automation:
-
Increases throughput/productivity
-
Reduces errors
-
Improves accuracy
-
Safety increases
-
Eliminates bottlenecks
-
Companies can scale up more easily
-
This makes workers more productive
-
This gives you visibility into what happens in the warehouse
-
Enhances customer experience
-
Improves employee satisfaction
-
It reduces downtime, and increases uptime
-
Quality products delivered on time
-
Eliminates human error
-
Assure compliance with regulations
Is there anything we should know about Manufacturing Processes prior to learning about Logistics.
No. You don't have to know about manufacturing processes before learning about logistics. Knowing about manufacturing processes will help you understand how logistics works.
What makes a production planner different from a project manger?
The major difference between a Production Planner and a Project Manager is that a Project Manager is often the person responsible for organizing and planning the entire project. While a Production Planner is involved mainly in the planning stage,
What does it take to run a logistics business?
To be a successful businessman in logistics, you will need many skills and knowledge. Effective communication skills are necessary to work with suppliers and clients. You need to understand how to analyze data and draw conclusions from it. You must be able manage stress and pressure under pressure. You must be creative and innovative to develop new ideas to improve efficiency. You need to have strong leadership qualities to motivate team members and direct them towards achieving organizational goals.
You should also be organized and efficient to meet tight deadlines.
Statistics
- In 2021, an estimated 12.1 million Americans work in the manufacturing sector.6 (investopedia.com)
- Job #1 is delivering the ordered product according to specifications: color, size, brand, and quantity. (netsuite.com)
- Many factories witnessed a 30% increase in output due to the shift to electric motors. (en.wikipedia.org)
- According to a Statista study, U.S. businesses spent $1.63 trillion on logistics in 2019, moving goods from origin to end user through various supply chain network segments. (netsuite.com)
- It's estimated that 10.8% of the U.S. GDP in 2020 was contributed to manufacturing. (investopedia.com)
External Links
How To
How to Use the 5S to Increase Productivity In Manufacturing
5S stands for "Sort", "Set In Order", "Standardize", "Separate" and "Store". Toyota Motor Corporation created the 5S methodology in 1954. It assists companies in improving their work environments and achieving higher efficiency.
The idea behind standardizing production processes is to make them repeatable and measurable. Cleaning, sorting and packing are all done daily. Because workers know what they can expect, this helps them perform their jobs more efficiently.
There are five steps that you need to follow in order to implement 5S. Each step requires a different action, which increases efficiency. Sorting things makes it easier to find them later. When you set items in an order, you put items together. You then organize your inventory in groups. Make sure everything is correctly labeled when you label your containers.
Employees must be able to critically examine their work practices. Employees must understand why they do certain tasks and decide if there's another way to accomplish them without relying on the old ways of doing things. They must learn new skills and techniques in order to implement the 5S system.
The 5S method not only increases efficiency but also boosts morale and teamwork. They feel more motivated to work towards achieving greater efficiency as they see the results.