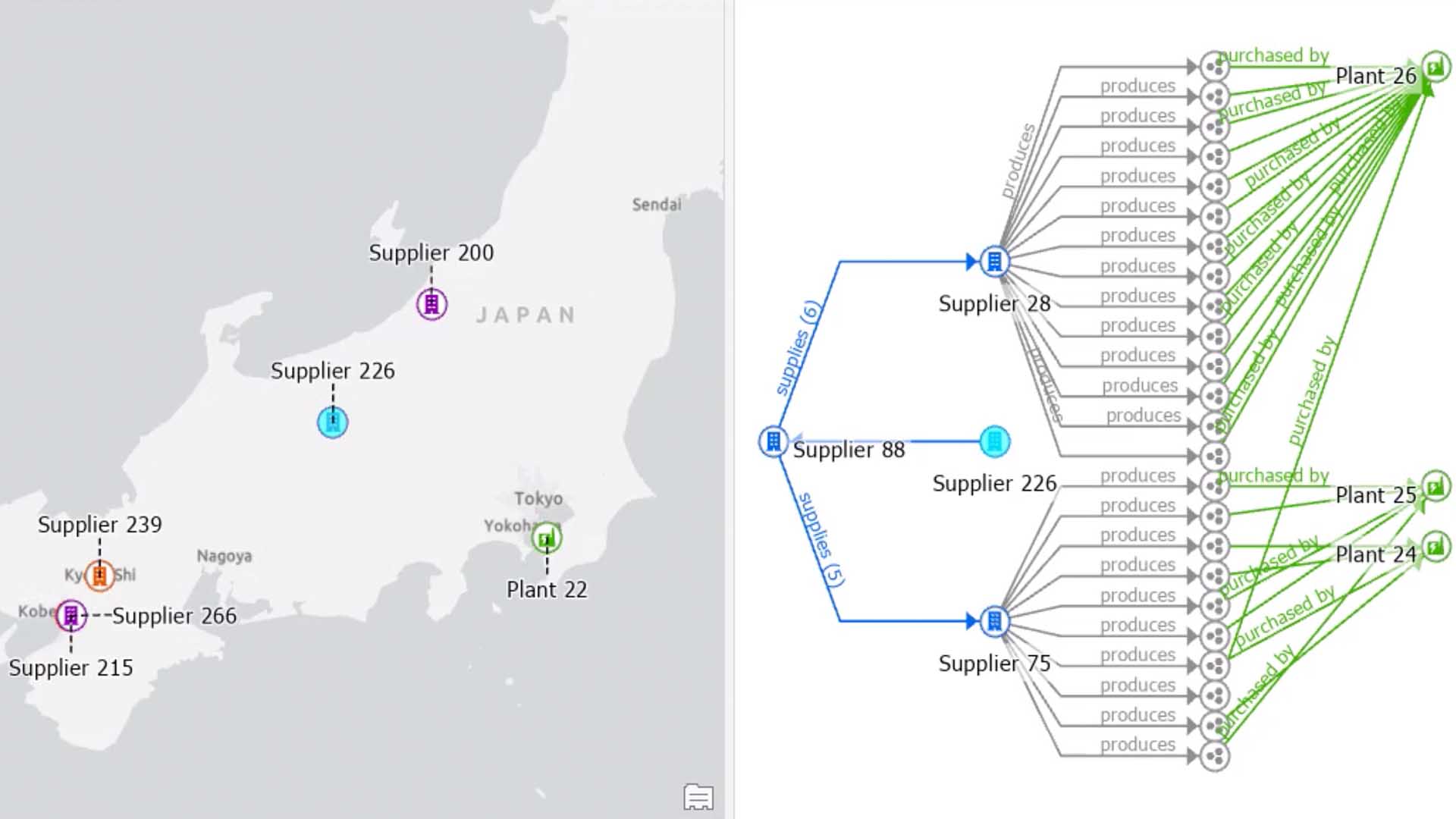
This is the place to go if you want news about manufacturing. Fusion 360 community members recap the week's events and share news about manufacturing innovation. The Fusion 360 community covers everything, from Alexandria Industries to Festo’s expansion plans. Fusion 360 covers a broad range of topics, from product launches to news about additive manufacture. Here are some recent articles regarding manufacturing innovation. Read on to learn more.
Alexandria Industries
Recent Alexandria Industries manufacturing news focuses their expansion in Douglas County, Minnesota. They currently have 480 employees, but the company plans to invest several million dollars in a new facility to expand their business. Alexandria Industries has long outpaced revenue growth and employment, but they are still having trouble finding qualified applicants for 50 of their new jobs. These positions pay $15-30 an hour, plus benefits. If you're interested in a new career, Alexandria Industries has a great opportunity for you!
Alexandria Industries recently promoted new management in order to support their growth. Jonathan D. Olson is the new CFO of Alexandria Industries. He is determined to invest in the company as well as the employees. He also joined the company as its new CFO, and is planning to improve the working conditions of employees and invest in training programs. Alexandria Plastics, Inc., the manufacturer of plastic injections and foam-molded components, will be incorporated into the new acquisition, which will allow the company to expand its capabilities.
Festo U.S. expansion plans
Festo Corp. has announced plans to expand its North American manufacturing operations. The company will increase its presence in Mason by three times and create 350 additional jobs. The expansion will add 350 jobs over five years and cost $90 million. Festo will provide support services as well as industrial training solutions. The expansion will also include a new Didactic Learning Center to serve manufacturing companies and colleges throughout the Tristate area.
The expansion will result in a new Mason, Ohio location dedicated to the manufacturing of automation components. The new facility will house both a Research and Development Center and Global Production Center. The new facility will house a Research and Development Center as well as a Global Production Center. The company also plans to create new jobs and establish a research and development center for automation technology. This expansion is part of a larger plan to focus on the U.S. market.
Additive Manufacturing
Manufacturers are beginning to recognize the advantages of additive manufacturing in their manufacturing processes, thanks to technological advancements. To reach the global marketplace, several companies have made partnerships. Voxeljet has partnered with AGC Ceramic, which is a ceramic and glass company. Voxeljet is partnering with AGC Ceramic to bring Brightorb, an innovative ceramic material, to the market and optimize VX1000 for 3D printing ceramic powder. Stratasys is also partnering with Tata Technologies to promote Indian additive manufacturing technologies.
New technologies are being developed to aid in the additive manufacturing process. Optimus 3D acquired a fourth Renishaw-based metal additive manufacturing system. The company also added metal powder to its 3D printing machine range. This development will ensure that additive manufacturing becomes an integral part advanced PLM. Advanced PLM will be more IoT-oriented, integrated, and flexible. These developments will enable rapid growth in many industries.
Collaborative manufacturing
What is collaborative Manufacturing? Collaborative Manufacturing is the direct input from the plant floor. This information is an important part of the management process. It involves interaction between the design and manufacturing team. Collaborative Manufacturing can improve productivity, quality, and reduce the number required to perform each production process. But what are the real benefits of collaborative production? Let's examine a few. How can collaboration in manufacturing help improve the performance of plants? Continue reading for more information.
Many industries embrace collaborative manufacturing. It is used for product development, product design improvement, inventory sync across the supply chain, and logistics cost reduction. Collaborative manufacturing can also reduce time-to market and volume and shorten the manufacturing cycle for designated suppliers. Collaborative manufacturing can bring significant benefits to everyone, so it is crucial for companies. However, it may not be right for all companies. Before adopting collaborative manufacturing, consider the benefits.
FAQ
Is automation important for manufacturing?
Automation is important not only for manufacturers but also for service providers. Automation allows them to deliver services quicker and more efficiently. In addition, it helps them reduce costs by reducing human errors and improving productivity.
What are the 4 types manufacturing?
Manufacturing is the process that transforms raw materials into useful products. It includes many different activities like designing, building and testing, packaging, shipping and selling, as well as servicing.
What can I do to learn more about manufacturing?
The best way to learn about manufacturing is through hands-on experience. But if that is not possible you can always read books and watch educational videos.
How can overproduction in manufacturing be reduced?
The key to reducing overproduction lies in developing better ways to manage inventory. This would reduce the time needed to manage inventory. This could help us free up our time for other productive tasks.
Kanban systems are one way to achieve this. A Kanbanboard is a visual tool that allows you to keep track of the work being done. Kanban systems are where work items travel through a series of states until reaching their final destination. Each state represents a different priority level.
If work is moving from one stage to the other, then the current task can be completed and moved on to the next. But if a task remains in the beginning stages it will stay that way until it reaches its end.
This allows you to keep work moving along while making sure that no work gets neglected. A Kanban board allows managers to monitor how much work is being completed at any given moment. This allows them to adjust their workflows based on real-time information.
Lean manufacturing is another option to control inventory levels. Lean manufacturing is about eliminating waste from all stages of the production process. Anything that doesn't add value to the product is considered waste. There are several types of waste that you might encounter:
-
Overproduction
-
Inventory
-
Packaging that is not necessary
-
Overstock materials
Manufacturers can reduce their costs and improve their efficiency by using these ideas.
Can some manufacturing processes be automated?
Yes! Yes! Automation has existed since ancient times. The Egyptians discovered the wheel thousands and years ago. Nowadays, we use robots for assembly lines.
There are many uses of robotics today in manufacturing. These include:
-
Robots for assembly line
-
Robot welding
-
Robot painting
-
Robotics inspection
-
Robots that create products
Manufacturing could also benefit from automation in other ways. 3D printing makes it possible to produce custom products in a matter of days or weeks.
Statistics
- In 2021, an estimated 12.1 million Americans work in the manufacturing sector.6 (investopedia.com)
- Job #1 is delivering the ordered product according to specifications: color, size, brand, and quantity. (netsuite.com)
- According to the United Nations Industrial Development Organization (UNIDO), China is the top manufacturer worldwide by 2019 output, producing 28.7% of the total global manufacturing output, followed by the United States, Japan, Germany, and India.[52][53] (en.wikipedia.org)
- In the United States, for example, manufacturing makes up 15% of the economic output. (twi-global.com)
- It's estimated that 10.8% of the U.S. GDP in 2020 was contributed to manufacturing. (investopedia.com)
External Links
How To
How to Use the Just In Time Method in Production
Just-intime (JIT), a method used to lower costs and improve efficiency in business processes, is called just-in-time. It allows you to get the right amount resources at the right time. This means that you only pay for what you actually use. Frederick Taylor was the first to coin this term. He developed it while working as a foreman during the early 1900s. He noticed that workers were often paid overtime when they had to work late. He then concluded that if he could ensure that workers had enough time to do their job before starting to work, this would improve productivity.
JIT is about planning ahead. You should have all the necessary resources ready to go so that you don’t waste money. It is important to look at your entire project from beginning to end and ensure that you have enough resources to handle any issues that may arise. You will have the resources and people to solve any problems you anticipate. This will prevent you from spending extra money on unnecessary things.
There are several types of JIT techniques:
-
Demand-driven JIT: You order the parts and materials you need for your project every other day. This will allow to track how much material has been used up. This will allow you to calculate how long it will take to make more.
-
Inventory-based: You stock materials in advance to make your projects easier. This allows one to predict how much they will sell.
-
Project-driven: This is an approach where you set aside enough funds to cover the cost of your project. If you know the amount you require, you can buy the materials you need.
-
Resource-based: This is the most common form of JIT. Here you can allocate certain resources based purely on demand. For example, if there is a lot of work coming in, you will have more people assigned to them. You'll have fewer orders if you have fewer.
-
Cost-based: This is similar to resource-based, except that here you're not just concerned about how many people you have but how much each person costs.
-
Price-based: This is similar to cost-based but instead of looking at individual workers' salaries, you look at the total company price.
-
Material-based: This approach is similar to cost-based. However, instead of looking at the total cost for the company, you look at how much you spend on average on raw materials.
-
Time-based JIT is another form of resource-based JIT. Instead of focusing only on how much each employee is costing, you should focus on how long it takes to complete your project.
-
Quality-based JIT: Another variation on resource-based JIT. Instead of worrying about the costs of each employee or how long it takes for something to be made, you should think about how quality your product is.
-
Value-based JIT: One of the most recent forms of JIT. In this instance, you are not concerned about the product's performance or meeting customer expectations. Instead, you're focused on how much value you add to the market.
-
Stock-based is an inventory-based system that measures the number of items produced at any given moment. This method is useful when you want to increase production while decreasing inventory.
-
Just-intime (JIT), planning is a combination JIT management and supply chain management. It's the process of scheduling delivery of components immediately after they are ordered. It's important because it reduces lead times and increases throughput.