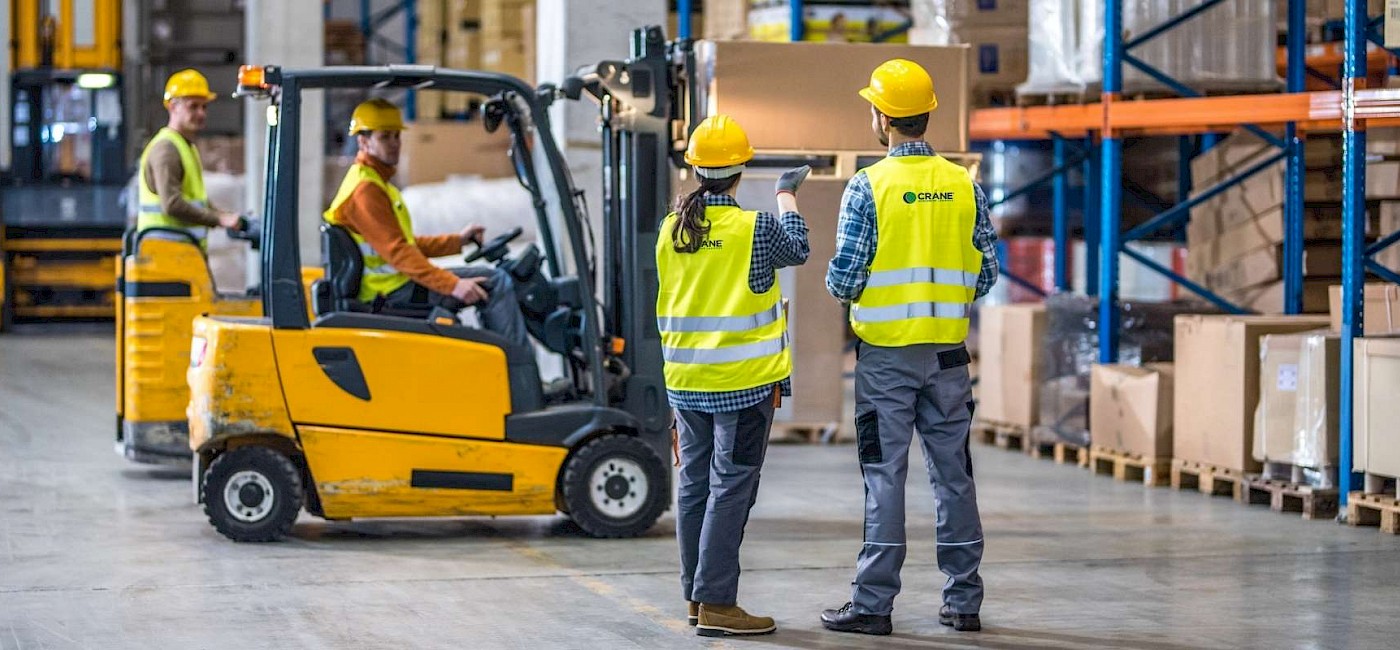
Occasionally, things go wrong, and we have to determine what caused them. The five whys is a technique that helps us to identify the root causes of problems.
The 5 Whys can help teams solve problems by helping them communicate. It stimulates curiosity in teams and helps them understand the perspectives of others so that they may work together to solve problems. It provides a system of interrogation that can be used when team members don't know why a problem occurred or how to fix it.
What is the Five Whys Method of Analysis?
The five whys is a quick and effective way to identify the root cause of any problem. The technique works best for simple to moderate problems but can also be used in complex cases.
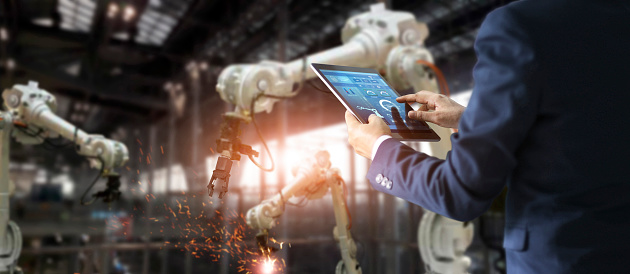
Depending on the type of problem, you may need to ask more than 5 whys. This is especially the case when there may be several root causes.
The 5 Whys Method: How to Use it
In order to complete a successful Five Whys Analysis, it is necessary to form a team with individuals who have a good understanding of the topic. You can bring together people from different industries and departments. It will enable them to offer a diverse range of perspectives and ideas that may help better pinpoint the root cause of any problem.
The team should then discuss the problem and ask each of the five questions. This will allow them to determine the root cause and whether there is a solution that can be implemented immediately or if a longer-term countermeasure should be taken.
Then they should carefully assess each question to determine if there is a reasonable response. This is a crucial step, as it gives the analyst confidence that he or she is on their way to a successful conclusion.
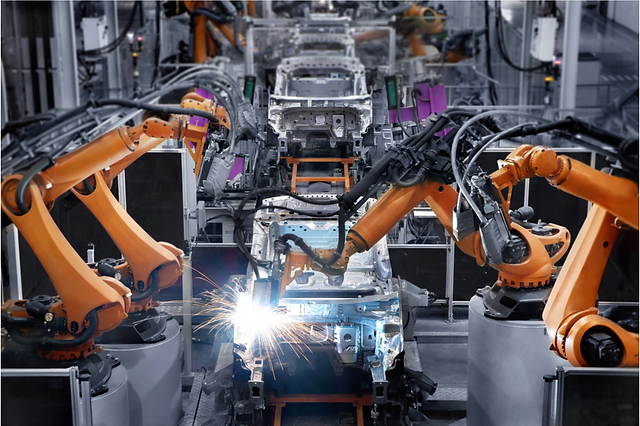
The five whys should be asked until the root cause is determined. They can then come up with countermeasures to prevent this issue from happening again. Once the root problem is identified, assign each corrective action to the person who will be responsible for it.
Use the five whys in order to find out what is at the core of any issue causing issues within your organization. It is especially effective when used along with other tools like FMEA or cause and effect analysis to better understand the root causes of a problem.
FAQ
What are manufacturing & logistics?
Manufacturing refers to the process of making goods using raw materials and machines. Logistics manages all aspects of the supply chain, including procurement, production planning and distribution, inventory control, transportation, customer service, and transport. Sometimes manufacturing and logistics are combined to refer to a wider term that includes both the process of creating products as well as their delivery to customers.
How can efficiency in manufacturing be improved?
First, identify the factors that affect production time. We must then find ways that we can improve these factors. If you don’t know how to start, look at which factors have the greatest impact upon production time. Once you have identified the factors, then try to find solutions.
What is it like to manage a logistics company?
To be a successful businessman in logistics, you will need many skills and knowledge. For clients and suppliers to be successful, you need to have excellent communication skills. You should be able analyse data and draw inferences. You must be able manage stress and pressure under pressure. To increase efficiency and creativity, you need to be creative. To motivate and guide your team towards reaching organizational goals, you must have strong leadership skills.
You should also be organized and efficient to meet tight deadlines.
Statistics
- Job #1 is delivering the ordered product according to specifications: color, size, brand, and quantity. (netsuite.com)
- (2:04) MTO is a production technique wherein products are customized according to customer specifications, and production only starts after an order is received. (oracle.com)
- In 2021, an estimated 12.1 million Americans work in the manufacturing sector.6 (investopedia.com)
- You can multiply the result by 100 to get the total percent of monthly overhead. (investopedia.com)
- According to the United Nations Industrial Development Organization (UNIDO), China is the top manufacturer worldwide by 2019 output, producing 28.7% of the total global manufacturing output, followed by the United States, Japan, Germany, and India.[52][53] (en.wikipedia.org)
External Links
How To
How to use 5S to increase Productivity in Manufacturing
5S stands in for "Sort", the "Set In Order", "Standardize", or "Separate". Toyota Motor Corporation created the 5S methodology in 1954. It improves the work environment and helps companies to achieve greater efficiency.
This approach aims to standardize production procedures, making them predictable, repeatable, and easily measurable. It means tasks like cleaning, sorting or packing, labeling, and storing are done every day. Through these actions, workers can perform their jobs more efficiently because they know what to expect from them.
Implementing 5S requires five steps. These are Sort, Set In Order, Standardize. Separate. And Store. Each step requires a different action, which increases efficiency. Sorting things makes it easier to find them later. Once you have placed items in an ordered fashion, you will put them together. Next, organize your inventory into categories and store them in containers that are easily accessible. Labeling your containers will ensure that everything is correctly labeled.
Employees will need to be more critical about their work. Employees need to be able understand their motivations and discover alternative ways to do them. To be successful in the 5S system, employees will need to acquire new skills and techniques.
The 5S method increases efficiency and morale among employees. They are more motivated to achieve higher efficiency levels as they start to see improvement.