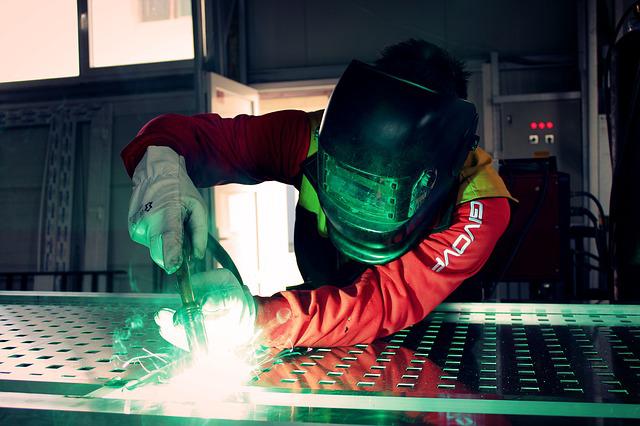
Lean to agile can be a great tool to reduce waste and improve team productivity. It emphasizes prioritizing work and eliminating waste. While empowering scrummasters and teams to do all the rest, it also focuses on prioritizing work. Also, agile teams should be empowered as product owners as well as servant leaders committed to the success and growth of their projects.
Time-to-market
Product success is measured by the time between ideation and full release. Your company will be able to capture more market share and generate more revenue if it is shorter. In order to improve this metric, companies must understand their development processes and resources. Then, they can refine their processes to meet their objectives and leverage their capabilities to improve time-to-market.
One way to reduce the time needed to market a product is to use outsourcing. A network of trusted supporting partners is another way to reduce time. This will help you reduce risk and to share your resources.
Iteration
Agile software development is all about iteration. Iteration is a key element of agile software development. This concept emphasizes the value of small, measured steps that can be evaluated faster than a complete process. The resulting features are better detailed, and the chances of success are higher. It is not always easy to do. Iterations should produce a running product that is easily accessible. This is possible by integrating, testing, and deploying the code on an internal server.
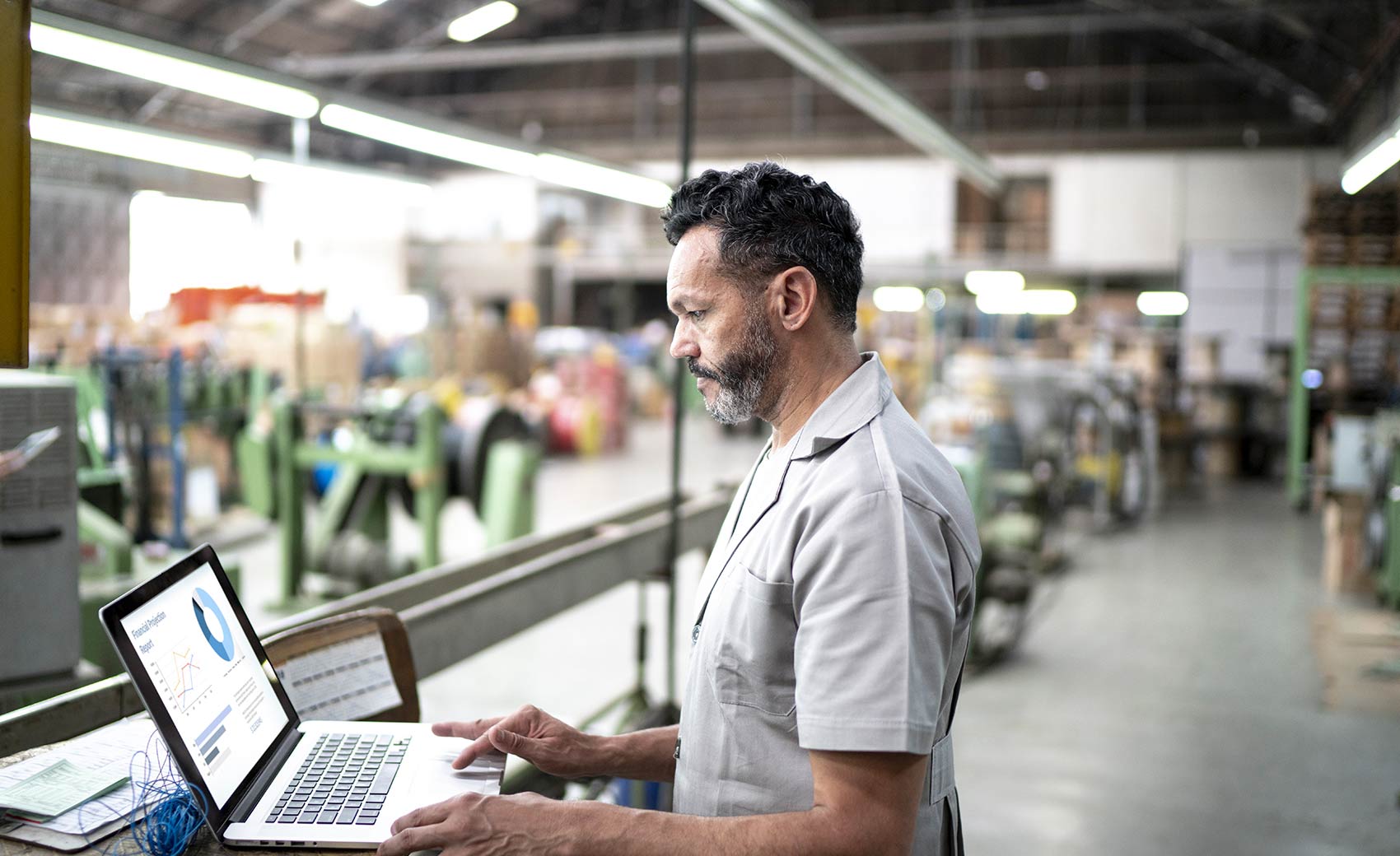
Iterations allow teams to refine their backlog, identify risks and fix them. The goal is for each iteration to improve on the previous one. Developers might modify or add features to existing functions. This continues until the product's release is complete.
Collaborative processes
Agile Manifesto stresses the importance of collaboration between developers and business stakeholders. This allows teams to prioritise work based upon business goals. Lean processes also promote a value stream - the end-to-end list of actions that produce the product or service customers desire. While these approaches may seem similar, there are important differences.
Agile is more flexible that Lean. Lean UX teams are more flexible than Lean, which uses rigid project management tools. Instead of working in large groups, they scale up quickly and work together to accomplish a goal. Agile is a system with small-world networks and deliverables. It emphasizes autonomy, exploration, collaboration, and teamwork. Agile approaches are required to scale from a single project into a multi-project program.
Implementing user research into agile groups
Agile teams are increasingly incorporating user research into their processes. This mindset is gaining popularity in product development, but it's also spreading to other areas. Teams are becoming more aware of the importance usability and user experience and the need to do quick and flexible research. Agile teams use agile thinking to find ways to connect with the product backlog to conduct user-centric research.
It is also essential to make user research workflows simpler and more democratized. This involves creating repeatable templates for user research that non-practitioners could use to run their tests. These templates should include the most important questions as well as cover all stages of product creation. To ensure consistent results, teams can also take advantage of UX platforms that offer preloaded templates and automated workflows.
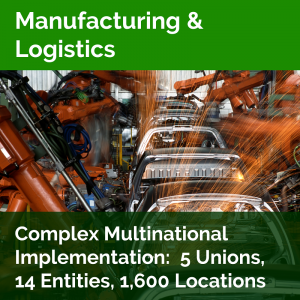
Value creation
Even though it is a simple concept, the idea of value creation can seem a little strange. You can create value in a narrower or wider scope. However, the process cannot be completely binary. In some cases, a narrower scope may create less value than a wide one, while a bigger scope can generate more value. Still, the concept of a full scope can be useful.
Lean and agile are two different ways to deliver a better product to customers. Combining these two methods allows companies to deliver better quality products faster. These two methods also reduce overhead because they empower employees to collaborate and concentrate on the customer's needs.
FAQ
What are the 7 Rs of logistics?
The 7R's of Logistics is an acronym for the seven basic principles of logistics management. It was published in 2004 by the International Association of Business Logisticians as part of their "Seven Principles of Logistics Management" series.
The acronym is made up of the following letters:
-
Responsible – ensure that all actions are legal and don't cause harm to anyone else.
-
Reliable - You can have confidence that you will fulfill your promises.
-
Use resources effectively and sparingly.
-
Realistic – consider all aspects of operations, from cost-effectiveness to environmental impact.
-
Respectful - show respect and treat others fairly and fairly
-
Resourceful - look for opportunities to save money and increase productivity.
-
Recognizable: Provide customers with value-added service
What are manufacturing and logistics?
Manufacturing is the process of creating goods from raw materials by using machines and processes. Logistics is the management of all aspects of supply chain activities, including procurement, production planning, distribution, warehousing, inventory control, transportation, and customer service. As a broad term, manufacturing and logistics often refer to both the creation and delivery of products.
How does a production planner differ from a project manager?
The major difference between a Production Planner and a Project Manager is that a Project Manager is often the person responsible for organizing and planning the entire project. While a Production Planner is involved mainly in the planning stage,
How can we reduce manufacturing overproduction?
It is essential to find better ways to manage inventory to reduce overproduction. This would reduce the time needed to manage inventory. By doing this, we could free up resources for other productive tasks.
This can be done by using a Kanban system. A Kanban board is a visual display used to track work in progress. Kanban systems are where work items travel through a series of states until reaching their final destination. Each state represents a different priority.
If work is moving from one stage to the other, then the current task can be completed and moved on to the next. It is possible to keep a task in the beginning stages until it gets to the end.
This keeps work moving and ensures no work is lost. Managers can see how much work has been done and the status of each task at any time with a Kanban Board. This allows them the ability to adjust their workflow using real-time data.
Lean manufacturing is another way to manage inventory levels. Lean manufacturing seeks to eliminate waste from every step of the production cycle. Any product that isn't adding value can be considered waste. These are some of the most common types.
-
Overproduction
-
Inventory
-
Unnecessary packaging
-
Material surplus
These ideas can help manufacturers improve efficiency and reduce costs.
What is the difference in Production Planning and Scheduling, you ask?
Production Planning (PP) refers to the process of determining how much production is needed at any given moment. Forecasting and identifying production capacity are two key elements to this process.
Scheduling is the process that assigns dates to tasks so they can get completed within a given timeframe.
How can manufacturing avoid production bottlenecks
You can avoid bottlenecks in production by making sure that everything runs smoothly throughout the production cycle, from the moment you receive an order to the moment the product is shipped.
This includes planning for both capacity requirements and quality control measures.
Continuous improvement techniques like Six Sigma are the best way to achieve this.
Six Sigma management is a system that improves quality and reduces waste within your organization.
It focuses on eliminating variation and creating consistency in your work.
What are the requirements to start a logistics business?
You need to have a lot of knowledge and skills to manage a successful logistic business. For clients and suppliers to be successful, you need to have excellent communication skills. You need to understand how to analyze data and draw conclusions from it. You must be able and able to handle stress situations and work under pressure. In order to innovate and create new ways to improve efficiency, creativity is essential. You need to have strong leadership qualities to motivate team members and direct them towards achieving organizational goals.
You must be organized to meet tight deadlines.
Statistics
- (2:04) MTO is a production technique wherein products are customized according to customer specifications, and production only starts after an order is received. (oracle.com)
- You can multiply the result by 100 to get the total percent of monthly overhead. (investopedia.com)
- In the United States, for example, manufacturing makes up 15% of the economic output. (twi-global.com)
- Job #1 is delivering the ordered product according to specifications: color, size, brand, and quantity. (netsuite.com)
- According to a Statista study, U.S. businesses spent $1.63 trillion on logistics in 2019, moving goods from origin to end user through various supply chain network segments. (netsuite.com)
External Links
How To
How to Use the 5S to Increase Productivity In Manufacturing
5S stands for "Sort", "Set In Order", "Standardize", "Separate" and "Store". Toyota Motor Corporation was the first to develop the 5S approach in 1954. It helps companies achieve higher levels of efficiency by improving their work environment.
This method aims to standardize production processes so that they are repeatable, measurable and predictable. This means that every day tasks such cleaning, sorting/storing, packing, and labeling can be performed. Because workers know what they can expect, this helps them perform their jobs more efficiently.
Implementing 5S requires five steps. These are Sort, Set In Order, Standardize. Separate. And Store. Each step requires a different action, which increases efficiency. You can make it easy for people to find things later by sorting them. When you set items in an order, you put items together. Once you have separated your inventory into groups and organized them, you will store these groups in easily accessible containers. You can also label your containers to ensure everything is properly labeled.
This requires employees to critically evaluate how they work. Employees need to understand the reasons they do certain jobs and determine if there is a better way. To implement the 5S system, employees must acquire new skills and techniques.
The 5S method not only increases efficiency but also boosts morale and teamwork. As they begin to see improvements, they feel motivated to continue working towards the goal of achieving higher levels of efficiency.