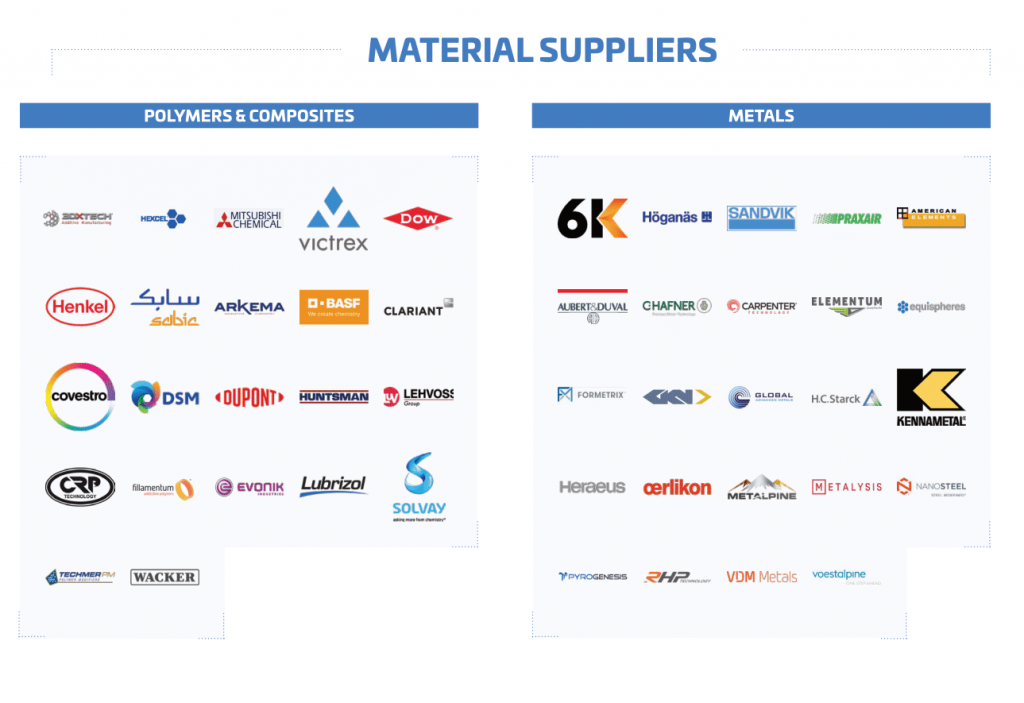
Non-value added activities are those that do not contribute to the product or service being produced. It might be necessary and useful, but it does nothing to directly increase the final product's worth. For example, if you want to cut lumber to the right dimensions, sharpening your saw is necessary. Sharpening your saw will not increase the product's value.
Understanding non-value-added activities requires that you first define value. Value can be defined as the amount customers will pay for a product/service. This value can vary depending upon the product or service offered. Adding value to a product or service is important for business success. If a company doesn't provide value, it won't last. In addition, a business will lose customers.
To determine if an action is value-added, ask yourself: "Does it add value to the product/service?" There are three possible answers. The first is to consider how the action relates to the value of the finished product. Another way is to evaluate how the action contributes to customer satisfaction. The final question is "Does this action improve the customer experience?"
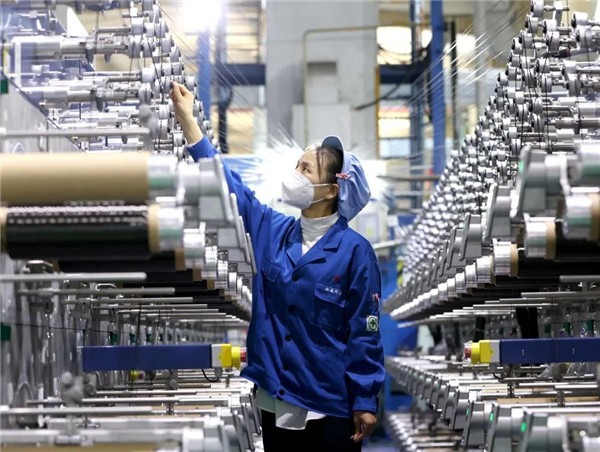
The definition of a value-added activity is one that demonstrates a positive return on investment. A value-added activity could be selling merchandise. Selling merchandise is an attractive activity as it can generate a profit for the company. Selling merchandise is an attractive activity because it helps to recover manufacturing costs.
Identifying a value-added activity is important, but it does not guarantee that the activity is successful. It is important that the value-added process meets customer expectations. The right process will ensure that the product or service arrives on time and is of high quality. Choosing the wrong process will result in delays or quality issues.
To identify a value-added activities, it is important to understand what a "non-valued" activity is. Non-valued activity is any task that does not affect the product's form or function. Checking, inspecting, billing, and processing are all examples of non-valued tasks.
Non-valued activities are activities that do not benefit the customer or contribute to their satisfaction. They are also activities that consume resources and incur expenses. It will help you improve the speed, quality and service level of your processes by identifying any wastes. Your cash flow and competitiveness will improve if you take steps to eliminate the waste.
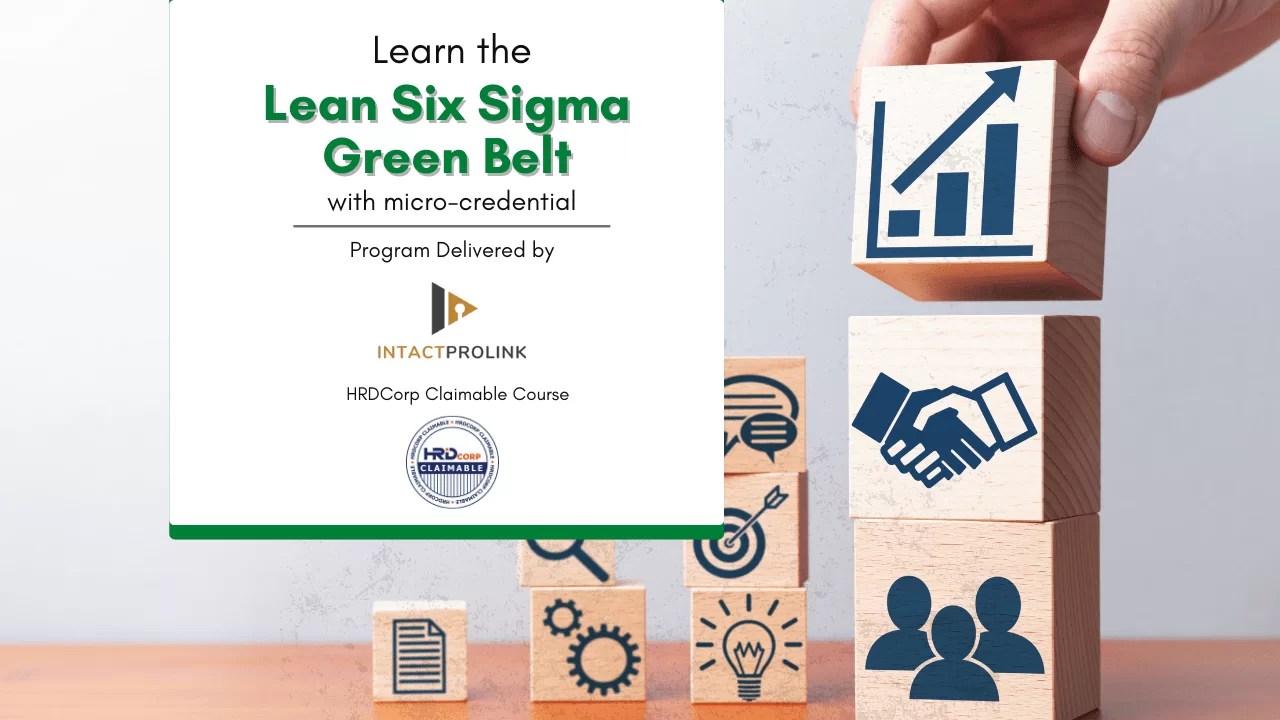
One of the most common mistakes is wasting time on non-value added activities. Non-valued activities include waiting, performing inspections and repairing defective products. Other activities that are not valuable to the finished product include copying documents, moving material, and filing paperwork.
To determine if your current process maximizes your potential, you can create a list of processes that will add value to the product/service. The process can be broken down to save time, money, and resources.
FAQ
What are the responsibilities of a logistic manager?
Logistics managers make sure all goods are delivered on schedule and without damage. This is achieved by using their knowledge and experience with the products of the company. He/she should make sure that enough stock is on hand to meet the demands.
Why automate your factory?
Modern warehousing is becoming more automated. The rise of e-commerce has led to increased demand for faster delivery times and more efficient processes.
Warehouses must be able to quickly adapt to changing demands. Technology investment is necessary to enable warehouses to respond quickly to changing demands. Automation warehouses can bring many benefits. Here are some reasons why it's worth investing in automation:
-
Increases throughput/productivity
-
Reduces errors
-
Improves accuracy
-
Safety is boosted
-
Eliminates bottlenecks
-
This allows companies to scale easily
-
This makes workers more productive
-
This gives you visibility into what happens in the warehouse
-
Enhances customer experience
-
Improves employee satisfaction
-
It reduces downtime, and increases uptime
-
This ensures that quality products are delivered promptly
-
Eliminates human error
-
This helps to ensure compliance with regulations
What are manufacturing and logistic?
Manufacturing refers to the process of making goods using raw materials and machines. Logistics covers all aspects involved in managing supply chains, including procurement and production planning. Manufacturing and logistics can often be grouped together to describe a larger term that covers both the creation of products, and the delivery of them to customers.
What are the 4 types manufacturing?
Manufacturing is the process by which raw materials are transformed into useful products through machines and processes. Manufacturing involves many activities, including designing, building, testing and packaging, shipping, selling, service, and so on.
What are the 7 Rs of logistics management?
The acronym "7R's" of Logistics stands for seven principles that underpin logistics management. It was developed and published by the International Association of Business Logisticians in 2004 as part of the "Seven Principles of Logistics Management".
The following letters make up the acronym:
-
Responsible - to ensure that all actions are within the legal requirements and are not detrimental to others.
-
Reliable - You can have confidence that you will fulfill your promises.
-
Be responsible - Use resources efficiently and avoid wasting them.
-
Realistic - Consider all aspects of operations, including environmental impact and cost effectiveness.
-
Respectful: Treat others with fairness and equity
-
You are resourceful and look for ways to save money while increasing productivity.
-
Recognizable: Provide customers with value-added service
Statistics
- According to the United Nations Industrial Development Organization (UNIDO), China is the top manufacturer worldwide by 2019 output, producing 28.7% of the total global manufacturing output, followed by the United States, Japan, Germany, and India.[52][53] (en.wikipedia.org)
- It's estimated that 10.8% of the U.S. GDP in 2020 was contributed to manufacturing. (investopedia.com)
- According to a Statista study, U.S. businesses spent $1.63 trillion on logistics in 2019, moving goods from origin to end user through various supply chain network segments. (netsuite.com)
- [54][55] These are the top 50 countries by the total value of manufacturing output in US dollars for its noted year according to World Bank.[56] (en.wikipedia.org)
- You can multiply the result by 100 to get the total percent of monthly overhead. (investopedia.com)
External Links
How To
How to use 5S in Manufacturing to Increase Productivity
5S stands as "Sort", Set In Order", Standardize", Separate" and "Store". Toyota Motor Corporation created the 5S methodology in 1954. It allows companies to improve their work environment, thereby achieving greater efficiency.
This method aims to standardize production processes so that they are repeatable, measurable and predictable. This means that tasks such as cleaning, sorting, storing, packing, and labeling are performed daily. Workers can be more productive by knowing what to expect.
Five steps are required to implement 5S: Sort, Set In Order, Standardize. Separate. Each step requires a different action, which increases efficiency. Sorting things makes it easier to find them later. You arrange items by placing them in an order. Once you have separated your inventory into groups and organized them, you will store these groups in easily accessible containers. Make sure everything is correctly labeled when you label your containers.
Employees need to reflect on how they do their jobs. Employees should understand why they do the tasks they do, and then decide if there are better ways to accomplish them. To implement the 5S system, employees must acquire new skills and techniques.
In addition to improving efficiency, the 5S system also increases morale and teamwork among employees. As they begin to see improvements, they feel motivated to continue working towards the goal of achieving higher levels of efficiency.