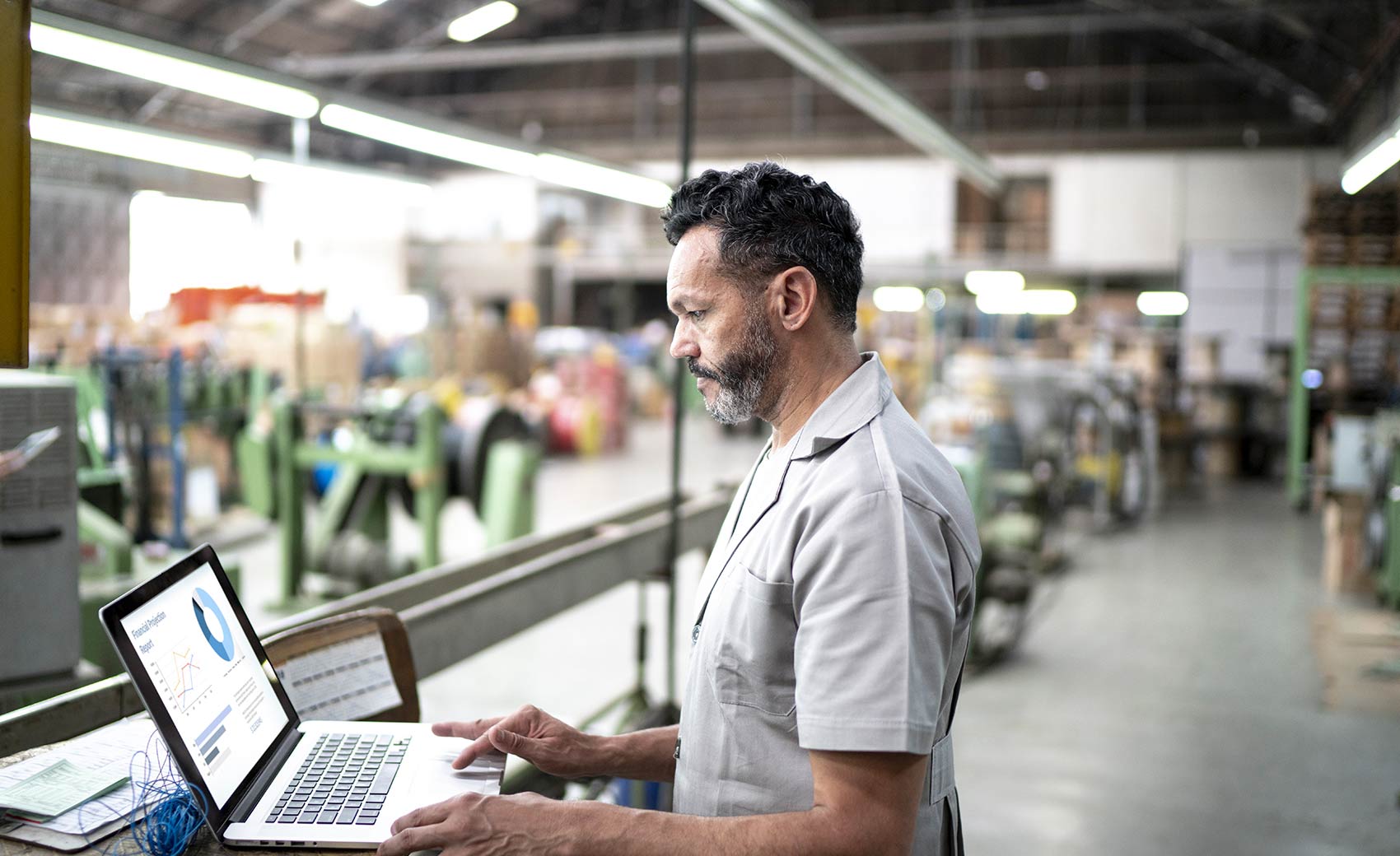
Amazon is searching for qualified Industrial Engineers to support their innovative and growing business. Industrial Engineers oversee the smooth and efficient operation of Amazon's processes. They use advanced analytical techniques to find and fix flaws in production processes. They work to ensure the company's products meet the highest quality standards.
Industrial engineers are responsible for designing, implementing, and maintaining efficient systems that integrate machines, materials, and workers. They study the manufacturing process to find ways to improve production and reduce waste. Also, industrial engineers are responsible for the design of new equipment and processes in order to increase productivity.
Also, industrial engineers are responsible for improving safety procedures within industrial facilities. They work with engineering principles to analyze problems and create solutions that make companies more profitable and efficient. There are many industries that industrial engineers can work in, including construction, transportation, energy, and manufacturing. A lot of industrial engineers are employed in the healthcare field.
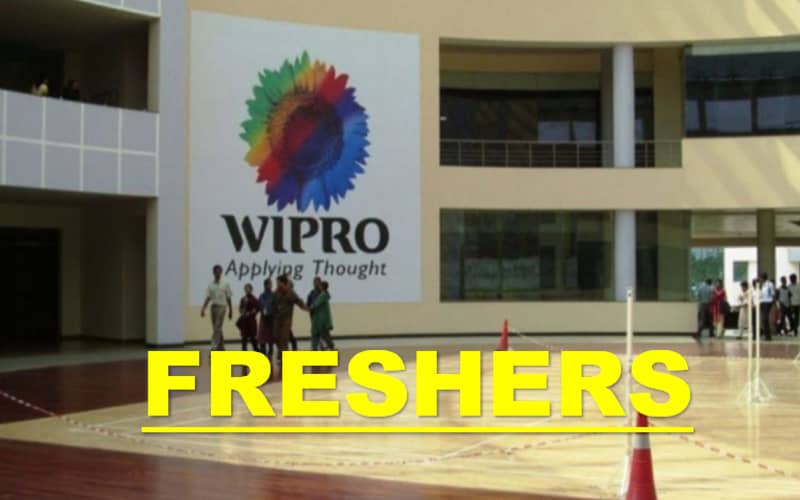
Industrial engineers often work in collaboration with other engineers to solve complex problems. These engineers often work long hours including weekends, holidays and nights. They are also people-oriented. They are resourceful and highly creative. They work hard to improve processes and reduce waste.
Industrial engineers can also be employed by consulting firms, manufacturing businesses, or research institutions. They can also work in transportation and logistics companies or the operations departments of companies. Depending on the industry, companies that are most appealing to industrial engineers include companies that produce products, or those that work on research projects.
Industrial engineers are expected to work on projects that have a business focus and will be compensated fairly. Most industrial engineers work 40 hours a week and may be required to work overtime on weekends or holidays. They are creative and resourceful and take pride in finding solutions that make their company more efficient.
Industrial engineers work in healthcare, manufacturing or transportation. Sometimes, they also work for consultants. These engineers are often employed to assist companies in all kinds of industries with improving their processes. They may also be employed by government agencies or research organisations. They may be interested in the human resource aspect of a company.
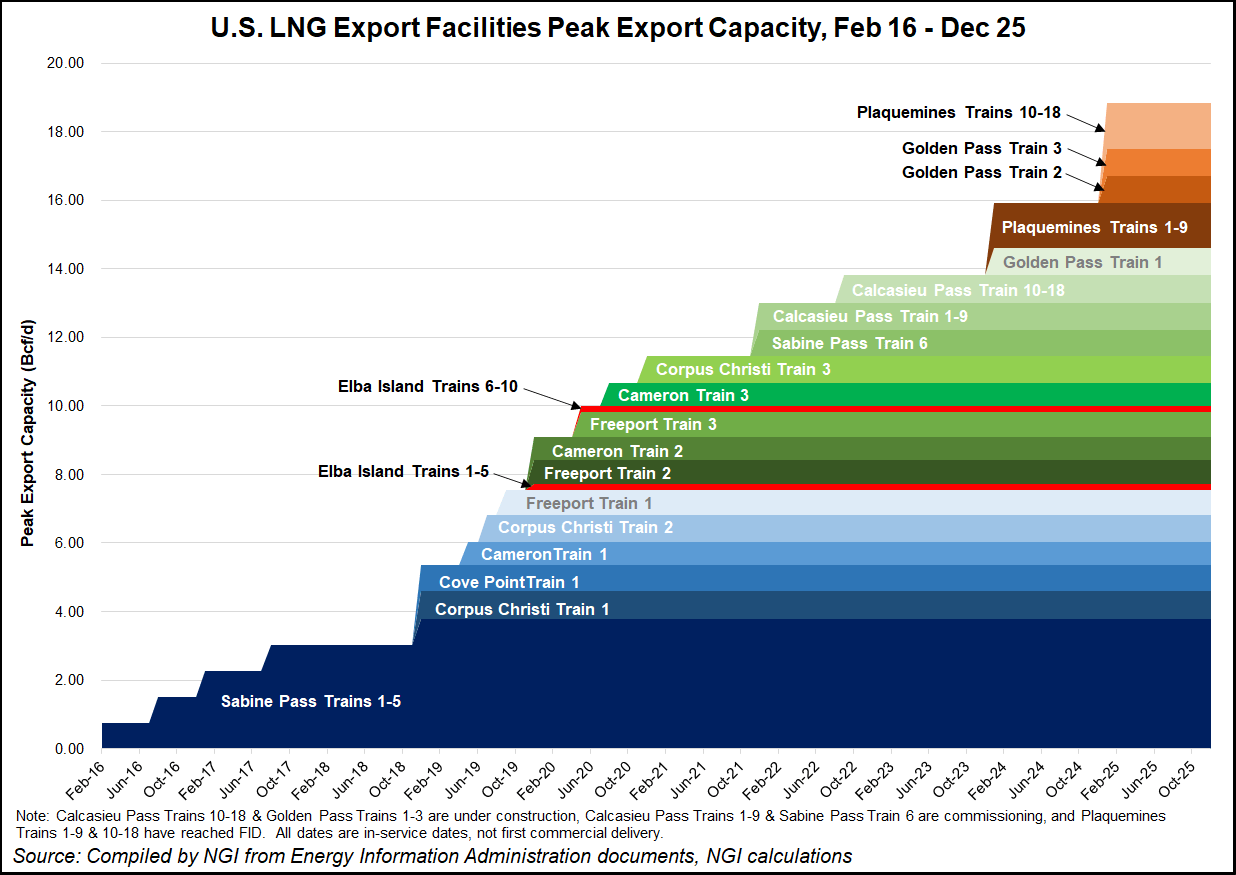
Industrial engineers have a high level of education and can expect to be paid a fair salary for their work. The average salary for entry-level industrial engineers is $63,000 to $85,000 depending on their position. Master's degrees may be necessary to have the best career options. A master's degree in engineering can increase your chances of staying in this industry.
Amazon's industrial engineers work on many different projects including manufacturing, logistics and technology. They also manage the engineering deliverables and help define projects. They are responsible for increasing efficiency in Amazon's fulfillment centers and warehouses, as well as ensuring that Amazon has the fastest routes between fulfillment centers.
FAQ
How does a production planner differ from a project manager?
The main difference between a production planner and a project manager is that a project manager is usually the person who plans and organizes the entire project, whereas a production planner is mainly involved in the planning stage of the project.
What is the responsibility of a production planner?
Production planners make sure that every aspect of the project is delivered on-time, within budget, and within schedule. They make sure that the product and services meet client expectations.
What are the 7 Rs of logistics management?
The acronym 7R's of Logistic is an acronym that stands for seven fundamental principles of logistics management. It was developed by International Association of Business Logisticians (IABL), and published as part of their "Seven Principles of Logistics Management Series" in 2004.
The following letters make up the acronym:
-
Responsible - ensure that actions are in compliance with legal requirements and do not cause harm to others.
-
Reliable – have faith in your ability and capability to keep promises.
-
It is reasonable to use resources efficiently and not waste them.
-
Realistic - Consider all aspects of operations, including environmental impact and cost effectiveness.
-
Respectful - Treat people fairly and equitably
-
Reliable - Find ways to save money and increase your productivity.
-
Recognizable provides value-added products and services to customers
What are the 4 types of manufacturing?
Manufacturing refers the process of turning raw materials into useful products with machines and processes. It involves many different activities such as designing, building, testing, packaging, shipping, selling, servicing, etc.
Statistics
- [54][55] These are the top 50 countries by the total value of manufacturing output in US dollars for its noted year according to World Bank.[56] (en.wikipedia.org)
- It's estimated that 10.8% of the U.S. GDP in 2020 was contributed to manufacturing. (investopedia.com)
- In the United States, for example, manufacturing makes up 15% of the economic output. (twi-global.com)
- You can multiply the result by 100 to get the total percent of monthly overhead. (investopedia.com)
- Many factories witnessed a 30% increase in output due to the shift to electric motors. (en.wikipedia.org)
External Links
How To
How to use lean manufacturing in the production of goods
Lean manufacturing is an approach to management that aims for efficiency and waste reduction. It was first developed in Japan in the 1970s/80s by Taiichi Ahno, who was awarded the Toyota Production System (TPS), award from KanjiToyoda, the founder of TPS. The first book published on lean manufacturing was titled "The Machine That Changed the World" written by Michael L. Watkins and published in 1990.
Lean manufacturing can be described as a set or principles that are used to improve quality, speed and cost of products or services. It is about eliminating defects and waste from all stages of the value stream. The five-steps of Lean Manufacturing are just-in time (JIT), zero defect and total productive maintenance (TPM), as well as 5S. Lean manufacturing seeks to eliminate non-value added activities, such as inspection, work, waiting, and rework.
Lean manufacturing not only improves product quality but also reduces costs. Companies can also achieve their goals faster by reducing employee turnover. Lean manufacturing has been deemed one of the best ways to manage the entire value-chain, including customers, distributors as well retailers and employees. Lean manufacturing is widely practiced in many industries around the world. Toyota's philosophy, for example, is what has enabled it to be successful in electronics, automobiles, medical devices, healthcare and chemical engineering as well as paper and food.
Five fundamental principles underlie lean manufacturing.
-
Define value - Find out what your business contributes to society, and what makes it different from other competitors.
-
Reduce Waste - Remove any activity which doesn't add value to your supply chain.
-
Create Flow. Ensure that your work is uninterrupted and flows seamlessly.
-
Standardize and Simplify – Make processes as consistent, repeatable, and as simple as possible.
-
Building Relationships – Establish personal relationships with both external and internal stakeholders.
Lean manufacturing, although not new, has seen renewed interest in the economic sector since 2008. Many companies have adopted lean manufacturing methods to increase their marketability. Some economists even believe that lean manufacturing can be a key factor in economic recovery.
Lean manufacturing is now becoming a common practice in the automotive industry, with many benefits. These include improved customer satisfaction, reduced inventory levels, lower operating costs, increased productivity, and better overall safety.
Lean manufacturing can be applied to almost every aspect of an organization. However, it is particularly useful when applied to the production side of an organization because it ensures that all steps in the value chain are efficient and effective.
There are three types of lean manufacturing.
-
Just-in-Time Manufacturing (JIT): This type of lean manufacturing is commonly referred to as "pull systems." JIT stands for a system where components are assembled on the spot rather than being made in advance. This approach aims to reduce lead times, increase the availability of parts, and reduce inventory.
-
Zero Defects Manufacturing, (ZDM): ZDM is focused on ensuring that no defective products leave the manufacturing facility. If a part is required to be repaired on the assembly line, it should not be scrapped. This applies to finished products, which may need minor repairs before they are shipped.
-
Continuous Improvement: Continuous Improvement aims to improve efficiency by continually identifying problems and making adjustments to eliminate or minimize waste. It involves continuous improvement of processes, people, and tools.