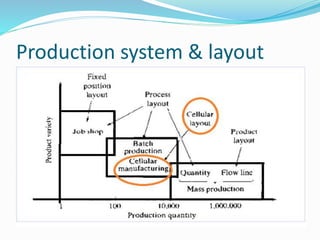
OSHA compliance is just as important as experience for food producers. Three things to look at when looking for a company to automate the production process.
Food manufacturers require experience
A high level of industry experience is often required for a position in a food manufacturer. But, those with no or little experience may still be able to find work. Many food manufacturers prefer to hire directly from within their ranks. A high school education may be helpful, but not necessarily necessary. As assistants to more skilled workers, entry-level employees begin as such. Then, they learn on the job. Some entry-level jobs are straightforward and can be completed in a few days. Some of the most common entry-level tasks include operating bread slicers. It is important to have experience in all areas of food manufacturing.
OSHA regulations must be followed
OSHA regulations regarding food manufacturers are enforced through an inspection. It can be initiated by an incident or complaint or a "programmed inspection". An OSHA enforcement visit at a yogurt manufacturing facility, for example, followed a complaint and was preceded by a planned inspection. In many cases, the citations include multiple violations of the process safety management standard, as well as standards on hazard communication, guarding machinery, stairs and platforms, emergency egress, forklift operation, hearing protection, and more.
Develop a plan for food safety
Most companies are subject to federal regulations. However, there are some exceptions. Although it is impossible, there are methods to prevent and manage possible hazards in food manufacturing. Food safety is not just a concern for the consumer's health, but can also be a problem for the business. Recalls can impact both the direct operations and those in the supply chains. Recalls can occur for many reasons including adulteration (misbranding) or violation of products. Food recalls are not only dangerous for the consumer, but can also be costly for food manufacturers.
Cost of automation
As utilities costs rise, automation is becoming more expensive for food manufacturers. Therefore, some regions have to import raw materials to keep up with local producers. Suppliers face declining profits as they pass the costs on to consumers. Automation can reduce production costs and improve efficiency. This article will explain how automation can improve food manufacturing's overall efficiency. You can also access our expertise in the industry.
Competing with established food companies presents challenges
To protect their market dominance, to prevent competition and to increase their profits, the top food companies use three main strategies. These strategies include the acquisition and development of valuable intangible asset, enforcement of production and marketing efficiencies, control over the supply chain, and monitoring and controlling costs. These strategies can create barriers to entry. These are some of the key challenges facing emerging food- and beverage companies. Let's take a closer look at each strategy.
FAQ
What are the products of logistics?
Logistics refers to the movement of goods from one place to another.
They cover all aspects of transportation, such as packing, loading, transporting and unloading.
Logisticians ensure that the product is delivered to the correct place, at the right time, and under safe conditions. Logisticians assist companies in managing their supply chains by providing information such as demand forecasts, stock levels and production schedules.
They monitor shipments in transit, ensure quality standards, manage inventories, replenish orders, coordinate with suppliers and other vendors, and offer support services for sales, marketing, and customer service.
Is automation necessary in manufacturing?
Automating is not just important for manufacturers, but also for service providers. It enables them to provide services faster and more efficiently. It reduces human errors and improves productivity, which in turn helps them lower their costs.
What are the responsibilities of a logistic manager?
Logistics managers ensure that goods arrive on time and are unharmed. This is done using his/her knowledge of the company's products. He/she also needs to ensure adequate stock to meet demand.
Statistics
- You can multiply the result by 100 to get the total percent of monthly overhead. (investopedia.com)
- (2:04) MTO is a production technique wherein products are customized according to customer specifications, and production only starts after an order is received. (oracle.com)
- It's estimated that 10.8% of the U.S. GDP in 2020 was contributed to manufacturing. (investopedia.com)
- Job #1 is delivering the ordered product according to specifications: color, size, brand, and quantity. (netsuite.com)
- In 2021, an estimated 12.1 million Americans work in the manufacturing sector.6 (investopedia.com)
External Links
How To
How to Use 5S for Increasing Productivity in Manufacturing
5S stands as "Sort", Set In Order", Standardize", Separate" and "Store". The 5S methodology was developed at Toyota Motor Corporation in 1954. It assists companies in improving their work environments and achieving higher efficiency.
This method aims to standardize production processes so that they are repeatable, measurable and predictable. It means tasks like cleaning, sorting or packing, labeling, and storing are done every day. Because workers know what they can expect, this helps them perform their jobs more efficiently.
There are five steps that you need to follow in order to implement 5S. Each step requires a different action to increase efficiency. For example, when you sort things, you make them easy to find later. You arrange items by placing them in an order. After you have divided your inventory into groups you can store them in easy-to-reach containers. Labeling your containers will ensure that everything is correctly labeled.
Employees will need to be more critical about their work. Employees need to be able understand their motivations and discover alternative ways to do them. To implement the 5S system, employees must acquire new skills and techniques.
In addition to increasing efficiency, the 5S method also improves morale and teamwork among employees. They will feel motivated to strive for higher levels of efficiency once they start to see results.